Brews For Thought:
The Brewster Consulting Group Blog
Search Our Blog:
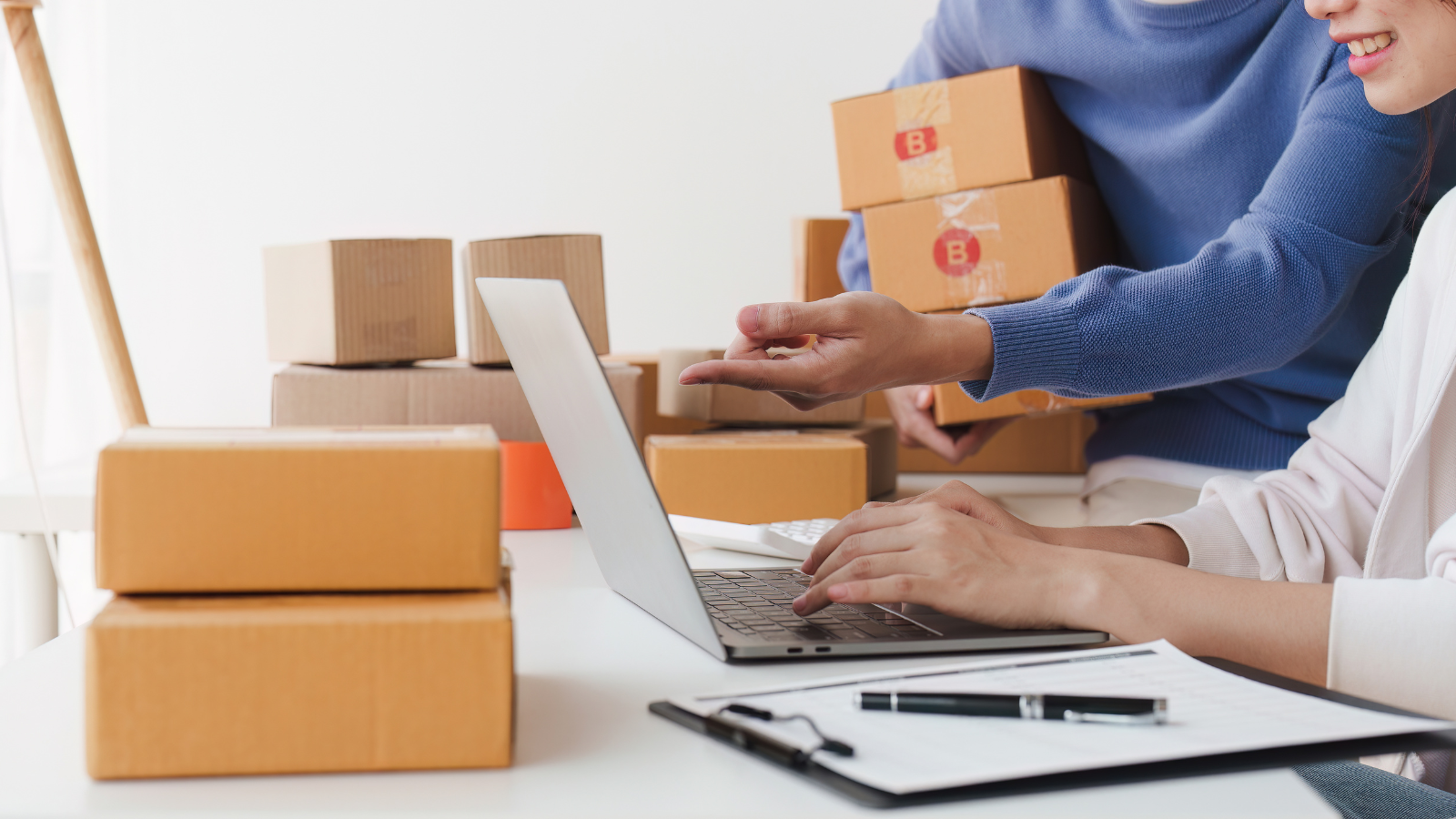
In this article, we’ll explore why small business project management is crucial, how structured project management methods prevent common pitfalls, and why even businesses with limited resources should prioritize it. What is Project Management? At its core, project management is the structured organization, execution, and completion of a project from start to finish. It’s a discipline that requires planning, coordination, and control to ensure successful outcomes. No matter the project – whether launching a new service, adopting new technology, or improving internal processes – successful execution follows a lifecycle with distinct phases: Initiation – Defining project goals, scope, and feasibility. Planning – Developing a roadmap, setting milestones, and identifying risks. Execution – Implementing the plan, managing tasks, and driving progress. Monitoring and Controlling – Tracking performance, making adjustments, and ensuring alignment with objectives. Closing – Evaluating success, documenting lessons learned, and finalizing the project. These phases, widely used in project management frameworks, provide structure, clarity, and direction – all crucial for small business success. Why Project Management is Even More Important for Small Businesses Larger companies typically have dedicated project managers or teams overseeing initiatives, ensuring projects stay on track. But in small businesses, leaders and employees often wear multiple hats, juggling responsibilities without a structured plan. Without proper project management, small businesses often face: Budget overruns – Lack of planning leads to unexpected costs. Missed deadlines – Without clear milestones, projects take longer than expected. Employee burnout – Teams get overwhelmed without a clear structure. Wasted resources – Poor planning leads to inefficiencies and lost productivity. Project failure – Without defined goals, execution can derail. Some small business owners may think, "We’re small; we don’t need formal project management." But size doesn’t dictate the need for structure. In fact, small businesses often need it more to ensure efficient growth, prevent wasted time, and maximize limited resources. Even businesses without the budget for a full-time project manager can use structured project management methods or work with a fractional project manager to gain expertise on an as-needed basis. How Project Management Prevents Failure: A CRM Implementation Example To illustrate the power of small business project management, let’s look at a common small business project: implementing a Customer Relationship Management (CRM) system. Scenario: A Small Business Wants to Implement a CRM Without Project Management Without structure project management, a business may: Choose the wrong CRM because they didn’t define clear goals. Struggle with data migration issues, leading to lost or duplicated customer records. Overspend due to poor budgeting and unexpected costs. Face low employee adoption because of lack of training or resistance to change. Fail to integrate the CRM properly with existing systems. Waste time and resources, ultimately abandoning the system. Scenario: A Small Business Uses Project Management for CRM Implementation If a business decides to approach this project with the tried-and-true project management method of using the five phases to do so, here’s how that might look: Initiation Phase (Defining the Project) Objective: Determine the need for a CRM and gain stakeholder buy-in. Identify challenges such as lost leads and inefficient follow-ups. Define project goals like tracking customer interactions and automate follow-ups. Create a budget and research software options. Gain leadership approval and document the project scope. Planning Phase (Creating the Roadmap) Objective: Develop a structured implementation plan. Select the best CRM (Salesforce, HubSpot, Zoho, etc.) Define project scope, timeline, and milestones. Assign roles (IT for integration, sales for testing, etc.) Identify risks such as staff resistance, technical issues, and any foreseeable migration issues. Create a training plan to ensure successful adoption. Execution Phase (Implementing the CRM) Objective: Deploy the CRM and begin usage. Purchase and install the CRM software. Migrate existing customer data carefully. Customize the CRM to align with business needs. Conduct initial employee training sessions. Launch a pilot program before full rollout. Monitoring & Controlling Phase (Tracking Progress and Adjustments) Objective: Ensure smooth operation and make improvements. Gather user feedback from employees. Track performance metrics such as response time and conversion rates. Address integration challenges and make system refinements. Provide additional training if needed. Closure Phase (Finalizing & Evaluating) Objective: Complete the project and assess its impact. Conduct a final project review. Document lessons learned and best practices. Hold a stakeholder meeting for feedback. Provide ongoing employee support. Transition to regular business operations. With this structured approach, the CRM implementation stays on budget, meets deadlines, and delivers measurable value to the business. What Small Businesses Gain from Project Management A well-managed project provides tangible benefits that improve business performance. Key advantages include: Time Management – Keeps the entire team aligned with clear deadlines. Streamlined Workflows – Ensures tasks are completed efficiently. Improved Stakeholder Communication – Enhances transparency and engagement. Higher Accountability – Ensures everyone knows their role and responsibilities. Risk Mitigation – Identifies challenges before they become major problems. Budget Control – Prevents overspending through careful planning. Where Should Small Businesses Start? If your small business has struggled with past projects or is preparing for a new initiative, structured project management is the key to success. Start by mapping out your project phases. Even a basic framework can prevent common mistakes. Use project management tools like Trello, Asana, or Monday.com to keep your team on track. Consider working with a fractional project manager to provide expertise without the cost of a full-time hire. Final Thoughts: Small Businesses Must Think Big with Their Projects Even if a business is small in size , its projects should not be treated that way. Structured project management lays the foundation for growth, efficiency, and long-term success. The right project management strategy can transform how small businesses operate, ensuring they grow, scale, and succeed with confidence. Does Your Business Have a Project Coming Up? Let’s talk about how structure project management can help you succeed! Head on over to our website to book a discovery call or to learn more about the project management services we offer!
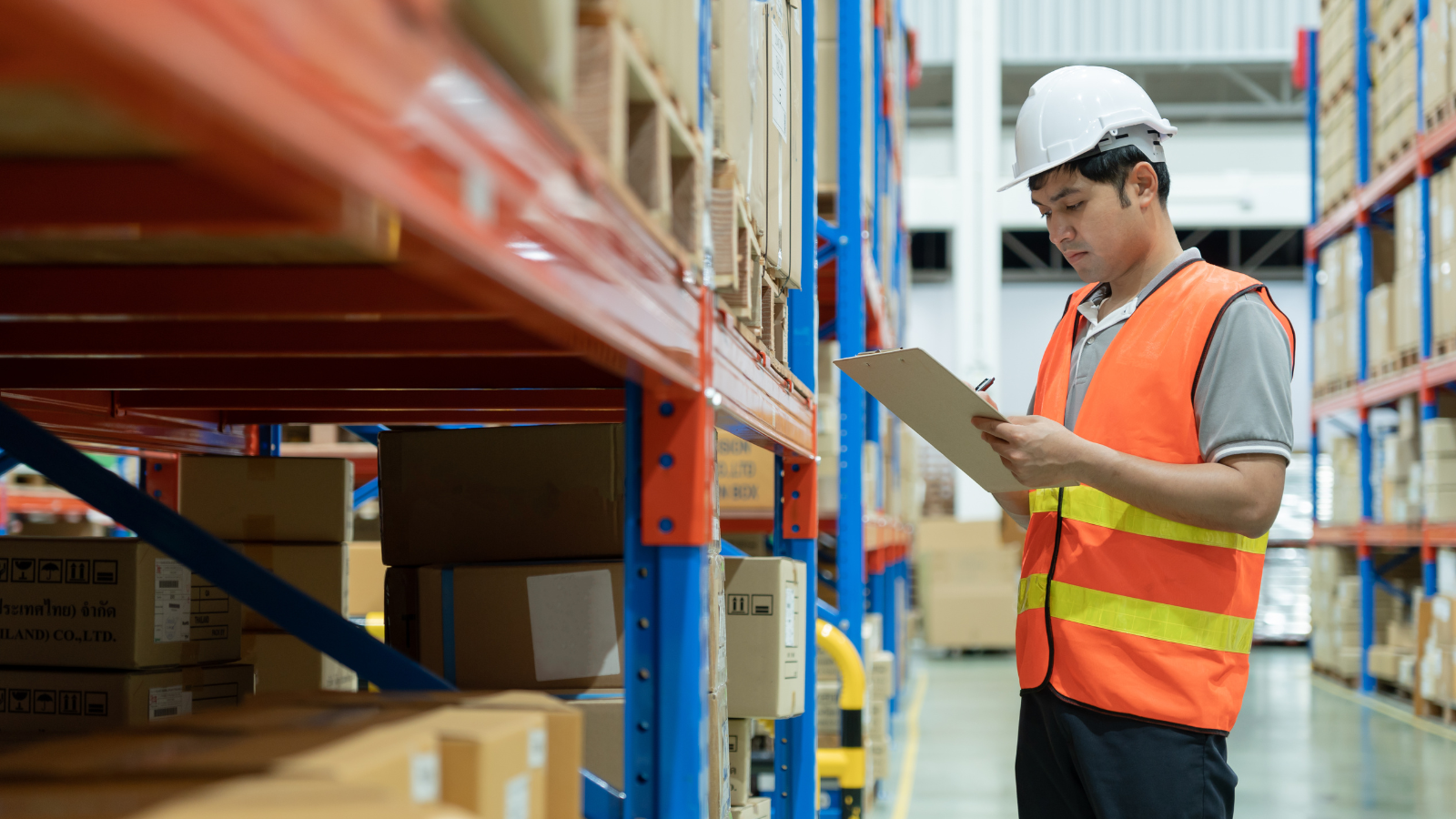
What is an Inventory Dashboard? In today’s fast-paced business environment, having the right tools at your disposal is critical to maintaining efficiency. Among the most valuable tools are dashboards—powerful solutions that enable businesses to collect, analyze, and visualize data across various departments. One of the most essential of these is inventory dashboard, designed to provide operations teams and managers with clear insights into workflow efficiency, inventory levels, and overall supply chain performance. Unlocking the Full Potential of Your Inventory Data An inventory dashboard goes beyond surface-level metrics, offering deep insights into operational efficiency and how well inventory performance aligns with key business objectives. By tracking key performance indicators (KPIs) , businesses can make more informed decisions and optimize their inventory management processes. Some of the most critical KPIs to monitor include: Inventory Turnover Rate – Measures how quickly inventory is sold and replaced within a given period. A high turnover rate indicates strong sales and efficient inventory management, while a low rate may suggest overstocking or slow-moving products. Fill Rate – Tracks the percentage of customer orders that are fulfilled from available stock without backorders or delays. A higher fill rate means better customer satisfaction and fewer lost sales. Stock-to-Sales Ratio – Compares available inventory to sales volume, helping businesses determine if they are overstocked or understocked relative to demand. Weeks on Hand (WOH) – Calculates how long current inventory levels will last based on historical sales data, helping businesses prevent stockouts or excessive inventory holding. Days Sales of Inventory (DSI) – Shows how many days, on average, it takes to sell inventory. A lower DSI indicates faster turnover and efficient inventory management. Supplier Lead Time – Measures the average time it takes for suppliers to deliver inventory after an order is placed, helping businesses optimize reorder points. By leveraging an inventory dashboard that monitors these KPIs in real time, businesses can proactively address supply chain challenges, reduce costs, and enhance overall operational efficiency. Additional Benefits of an Inventory Dashboard Inventory dashboards can be tailored to meet the specific needs of each business, but across industries, they consistently deliver the following benefits: Identifying opportunities for cost savings Gaining real-time visibility into inventory control Ensuring accuracy in inventory records Understanding customer purchasing behavior Improving demand forecasting and trend analysis Identifying areas needing inventory adjustments Evaluating operational efficiency Customizing dashboard features to align with business goals Types of Inventory Dashboards Depending on the complexity of your operations, inventory dashboards can take various forms. Some of the common inventory dashboards include: Supplier Performance Dashboard – Tracks supplier reliability, lead times, and order fulfillment rates. Product-Specific Dashboard – Focuses on individual products, providing insights into sales performance, demand fluctuations, and stock availability. Location-Based Dashboard – Monitors inventory movement and stock levels across multiple warehouses, retail stores, or distribution centers. While some businesses prefer a comprehensive inventory dashboard that integrates all of these elements, others opt for specialized dashboards tailored to different departments or leadership roles for more targeted insights. Below is an example of an inventory dashboard created for one of our manufacturing clients that was customized to fit their needs:
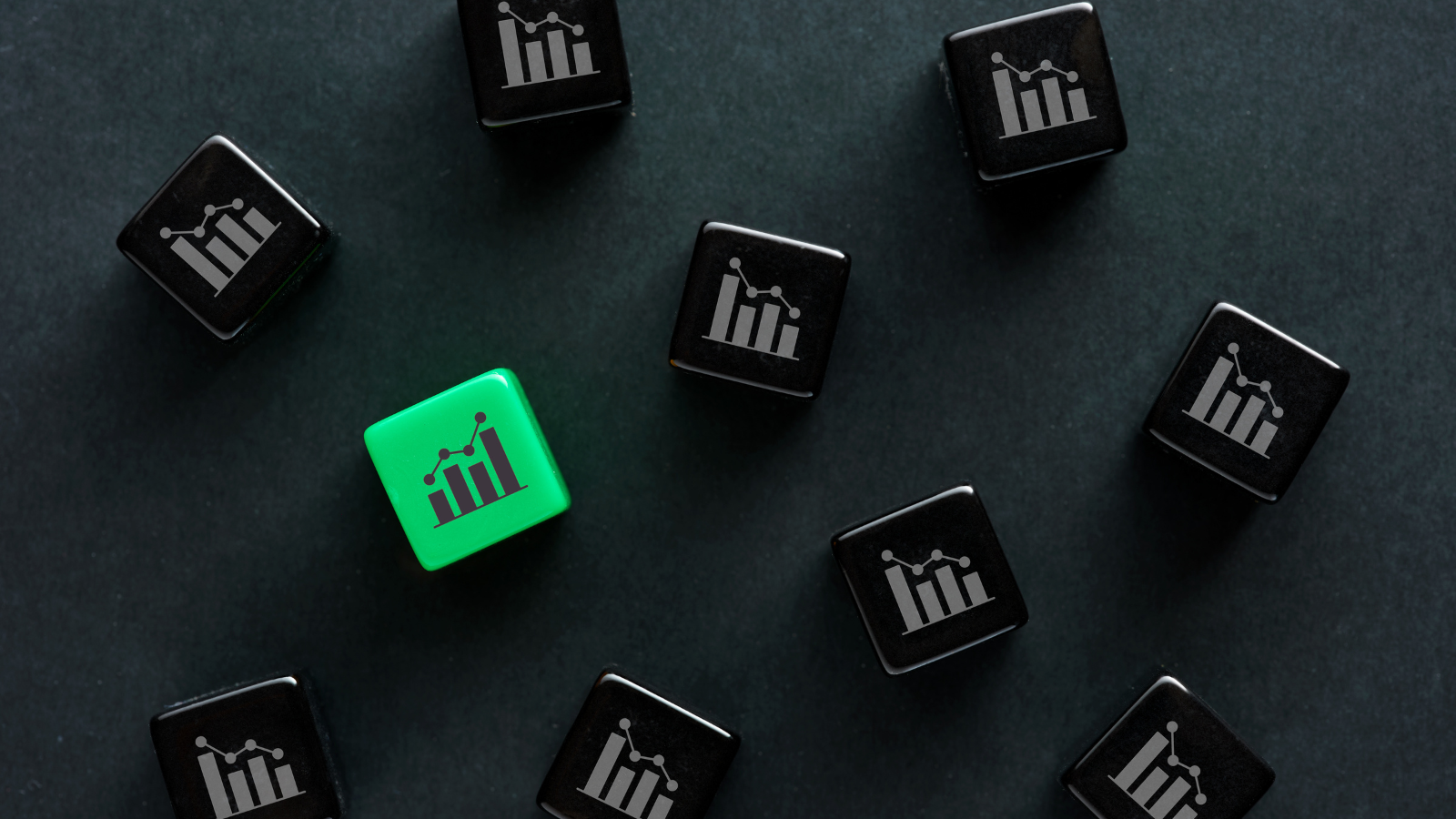
One of the most important aspects of process mapping is ensuring a clear and well-defined scope . Without the necessary context, process maps can become incomplete or misaligned with business objectives. Another common mistake is an imbalance in detail—some areas may be overly complex while others lack essential information. A well-structured process map provides the right level of detail to guide users without overwhelming them. Maintaining consistency in symbols and notation is also essential, especially when mapping multiple processes. Standardizing these elements ensures clarity across different departments and prevents misinterpretation. Engaging the right stakeholders in the process is crucial. Those who actively participate in or oversee a process have the best insights into how it functions and can provide valuable input. Their involvement helps create accurate, practical maps that truly reflect business operations. Additionally, when a process is particularly complex, it may be beneficial to divide it into multiple maps, separating larger workflows into smaller, more manageable components. This prevents confusion and ensures that each aspect of the process is thoroughly documented without unnecessary complexity. Once developed, process maps must be regularly reviewed and updated. Business operations evolve, and failing to adjust process documentation accordingly can render them obsolete. Testing and validating process maps before final implementation is another critical step. Running through the process in real-world scenarios can reveal gaps or inefficiencies that need to be addressed. Moreover, clarity in process steps is essential—being too vague can leave employees uncertain about their tasks, while excessive detail can lead to unnecessary complications. Striking the right balance ensures that process maps remain effective. Beyond initial implementation, continuous feedback from employees and stakeholders ensures that process maps remain relevant and user-friendly . If a business invests time and resources in developing process documentation, it must also ensure that these maps are actively used and provide tangible benefits. Otherwise, the effort becomes a waste of time, energy, and money. When Should a Business Implement Process Mapping? While process mapping can be valuable at any time, there are specific scenarios where it becomes particularly important. Businesses that are focused on achieving specific goals often use process maps to create a structured approach to reaching their objectives. Defining processes clearly can help ensure consistency, efficiency, and alignment with strategic priorities. Periods of growth, restructuring, or workforce changes also present an ideal time for process mapping. Whether hiring new employees, promoting staff, or reorganizing roles, businesses need clear documentation to help employees understand their responsibilities and approach their duties effectively. Without well-defined processes, teams may struggle with inefficiencies, miscommunication, and inconsistencies in execution. In some cases, businesses find themselves stagnating , unable to meet key performance targets or struggling with inefficiencies . When operations seem unclear or disconnected, process mapping can help identify areas for improvement. Working with an expert to analyze workflows and create structured documentation can bring clarity, uncover inefficiencies, and highlight areas where additional training or support may be necessary. Even for businesses that are not experiencing significant operational challenges, having well-documented processes provides a layer of insight that supports decision-making and long-term strategic planning. Signs Your Process Maps May Not Be Working Even if a business has documented processes, that does not necessarily mean they are being used effectively . One common issue is poor communication across teams. If employees, departments, and leadership are not aligned, processes may break down due to misunderstandings or lack of clarity. Regular communication and process reviews are essential to maintaining accurate, functional documentation. Another challenge arises when process maps focus too much on what should be avoided rather than providing clear instructions on what should be done. Employees need actionable guidance, not just a list of what not to do. Similarly, if different employees interpret the same process map in different ways, it could indicate that the documentation lacks clarity. Ensuring that process maps are easy to follow and understood by all team members is key to consistency in execution. A disconnect between documented processes and actual business operations is another warning sign. If employees are still unsure of their responsibilities despite having process documentation, it may indicate that the maps lack clarity regarding who should perform each task. Assigning accountability and verifying that employees understand their roles helps ensure that documented processes translate into real-world efficiency. Optimizing Process Mapping with Expert Support Developing and maintaining effective process maps is a complex task, and many businesses find it beneficial to seek external support. A consulting firm specializing in process improvement can provide an objective perspective, helping to analyze existing workflows and identify areas for enhancement. Their expertise ensures that process maps are structured effectively, align with best practices, and serve as valuable tools for business operations. Additionally, experienced consultants can provide guidance on implementing and maintaining process maps to ensure they remain practical and relevant. Businesses that invest in professional support for process mapping can expect better alignment with strategic goals, improved operational efficiency, and enhanced clarity in workflows. By leveraging external expertise, organizations can maximize the benefits of process mapping and create a foundation for sustained success. If you are ready to revamp or create process maps for your business, don’t hesitate to reach out to one of our consultants. Visit our process documentation page to learn more about how we can provide you with process maps that will enhance and streamline your operations.
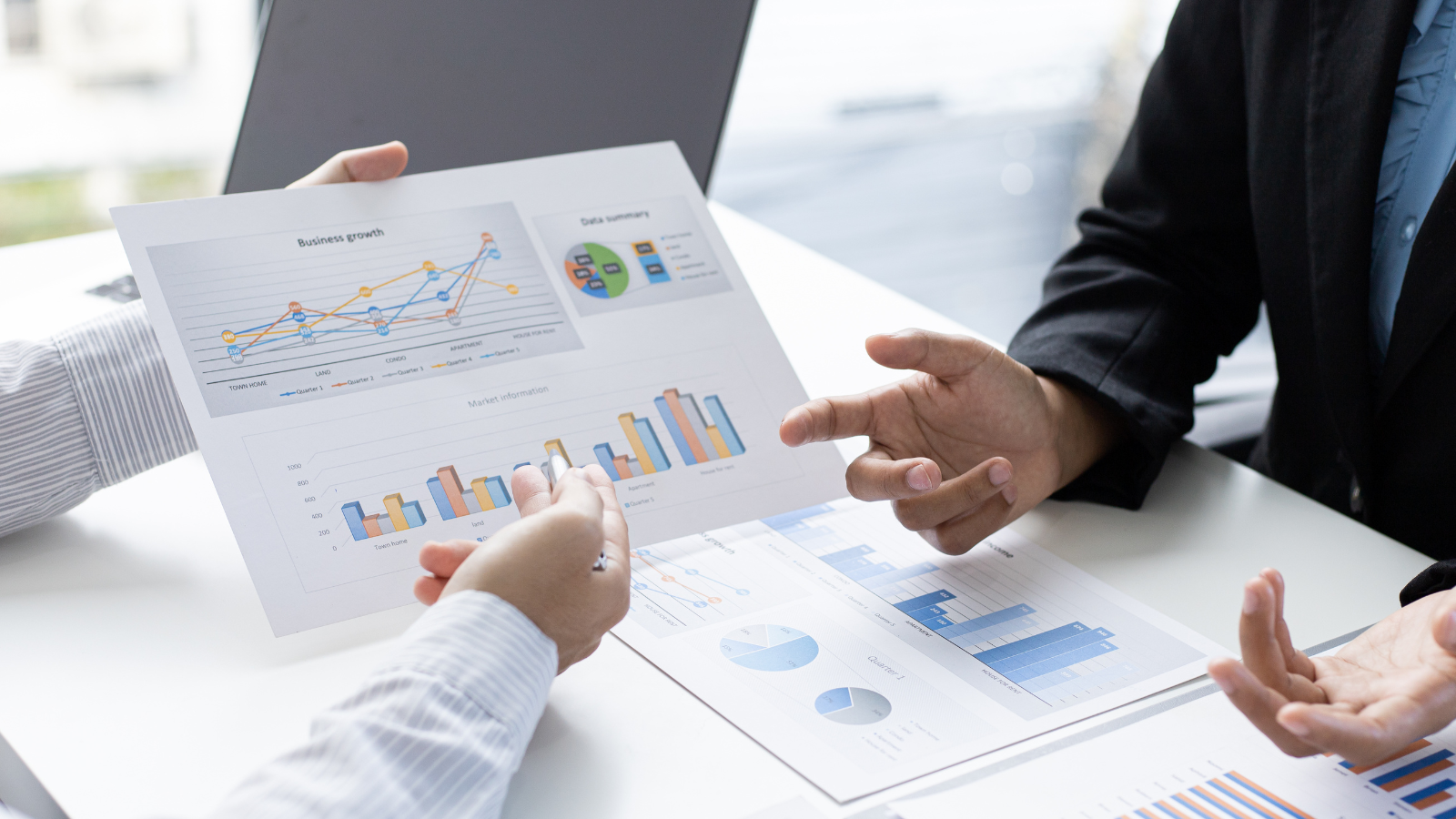
But what makes this the right choice for so many organizations? Understanding what draws businesses to these consultants—and what they hope to achieve—can provide valuable insight into their role and impact. If your company is exploring the idea of working with a business improvement consultant, it’s important to first understand their value and why so many businesses consider them a critical part of their growth strategy. Gaining this insight will help you determine whether this approach aligns with your organization's needs and long-term goals. A Business Improvement Consultant is a seasoned professional who collaborates with organizations to identify areas for improvement, implement strategic frameworks, and drive operational efficiencies to support business growth and long-term success. Key Responsibilities of a Business Improvement Consultant: Identifying Challenges and Opportunities: Analyze business operations to uncover inefficiencies, bottlenecks, and pain points. Conduct thorough assessments of current challenges and areas that require improvement to ensure alignment with organizational objectives. Developing and Implementing Solutions: Evaluate identified issues and develop tailored, actionable strategies that align with the company's goals. Lead the implementation of these strategies to address key concerns and drive measurable improvements. Facilitating Organizational Alignment: Support cross-functional collaboration by conducting training sessions, facilitating interdepartmental discussions, and ensuring all stakeholders are aligned with the business improvement initiatives. Foster a culture of accountability and clear communication to drive organizational buy-in. Providing Ongoing Support and Innovation: Offer continuous guidance, recommendations, and insights to support sustainable growth. Assist in the integration of new technologies and processes that enhance operational efficiency and competitiveness. Enhancing Market Strategies: Work closely with the sales and marketing teams to analyze new and existing markets. Provide insights that align with the organization’s strategic objectives, improve market positioning, and enhance the company's online presence. Coaching Leadership Teams: Provide strategic advice and mentorship to business leaders, identifying potential roadblocks and offering proactive solutions to navigate challenges effectively. Managing Organizational Change: Support change management initiatives, including workforce transitions, by developing structured plans to ensure smooth implementation and minimal disruption to business operations. Monitoring and Mitigating Risks: Proactively track potential risks and setbacks, ensuring they are managed effectively to prevent undue strain on other areas of the business. Develop contingency plans to address unforeseen challenges. These are just a few of the key areas where a business improvement consultant can provide valuable support. When determining whether to engage a consultant, businesses should assess their current challenges and evaluate whether external expertise could offer the solutions they need. Below are some of the most common challenges businesses face when considering the need for a business improvement consultant: Internal Operational Challenges: Companies may struggle with making strategic decisions due to a lack of resources, expertise, or persistent operational inefficiencies that hinder growth and productivity. Overworked or Underqualified Staff: Employees may already be stretched thin, or they may lack the necessary skills to effectively address critical business challenges—particularly in areas requiring specialized knowledge, such as technology and process optimization. Ensuring that workloads are balanced, and staff are properly equipped is essential for sustainable operations. Ineffective Internal Solutions: Businesses may have attempted to resolve ongoing issues internally without success, leading to frustration and stagnation. When internal efforts fail to yield results, external expertise can provide a fresh, results-driven approach. Cost-Effectiveness Considerations: Determining the most cost-efficient approach—whether to continue investing time and resources internally or to hire a consultant with the knowledge and experience to implement effective solutions quickly—can be a critical factor in the decision-making process. Lack of Fresh Perspectives: If a business has exhausted its internal strategies without achieving meaningful progress, bringing in an external consultant can offer a fresh perspective and innovative solutions that may not have been previously considered. Companies facing these challenges and choosing to partner with a business improvement consultant often experience a range of significant benefits. If your business is considering this path, the following advantages illustrate what could be achieved through expert guidance and strategic support: Access to Expertise and Fresh Perspectives: A business improvement consultant brings a wealth of knowledge, innovative ideas, and industry insights that can be directly applied to address your organization’s unique challenges. Their experience enables them to identify opportunities that may not be apparent internally. Accelerated implementation and Growth: With a consultant’s expertise, businesses can implement strategies and action plans more efficiently and effectively. This leads to quicker resolutions of operational issues and helps propel the organization to the next level of success. Enhanced Decision-Making Confidence: Working with a business improvement consultant provides greater clarity and stability in decision-making. Business leaders can make more informed choices with the assurance that operational challenges are being addressed, reducing wasted resources and ensuring a clear plan for future growth. Flexible and Cost-Effective Engagements: Engaging a consultant offers flexibility in terms of time and scope. Businesses can leverage their expertise for specific projects, short-term initiatives, or long-term strategic support—allowing for cost-effective solutions without the commitment of a full-time resource. Industry-Specific Insights and Best Practices: A consultant with experience across various industries brings valuable insights and proven strategies that have successfully addressed similar challenges in other organizations. This external perspective can be instrumental in driving meaningful improvements. Long-Term Knowledge and Sustainable Improvements: Beyond immediate problem-solving, businesses benefit from lasting organizational improvements. Consultants equip teams with the necessary tools, processes, and understanding to continue addressing challenges independently, fostering better communication, collaboration, and operational efficiency. We’ve explored what a business improvement consultant does and the many benefits they can bring to an organization. But how do you find the right consultant for your business? A business improvement consultant will take on significant responsibilities, requiring access to sensitive information, financial resources, and valuable time. Since the goal of hiring a consultant is to resolve existing challenges and optimize operations, it’s crucial to choose the right partner to avoid further resource misallocation. To help guide your search, here are key factors to consider when selecting the ideal business improvement consultant: Comprehensive Business Acumen: The consultant should demonstrate a deep understanding of how businesses operate and engage in meaningful discussions about your company’s unique processes, challenges, and goals. Strong Analytical Capabilities: A successful consultant must possess exceptional analytical skills to assess your business needs effectively and determine the appropriate improvement methodologies and strategies to implement at the right time. Proven Track Record and Reliability: Look for a consultant with a history of successful engagements, a desire to see your business thrive, and the ability to follow through on commitments. Their previous work experience should serve as a testament to their capabilities. Effective Communication and Listening Skills: The right consultant should be an active listener who takes the time to understand your business challenges thoroughly. They should demonstrate a genuine interest in your success and a commitment to providing tailored solutions. Project Management Expertise: Familiarity with project management principles is essential to ensure a structured approach to business improvement initiatives. The consultant should be dedicated to delivering the level of support and guidance your organization requires. We hope this guide provides valuable insights to help you make an informed decision when selecting a business improvement consultant. It’s important to know what to look for and what questions to ask when evaluating potential consultants. At Brewster Consulting Group , we embody these qualities and are committed to helping businesses overcome challenges and achieve sustainable growth. We would love the opportunity to discuss your unique needs and explore how our tailored solutions can drive your business forward. Ready to take the next step? Contact us today to schedule a consultation and let’s start building a path to success together. If you’re not quite ready to speak with our team, visit our website to learn more about our approach and how we can help.
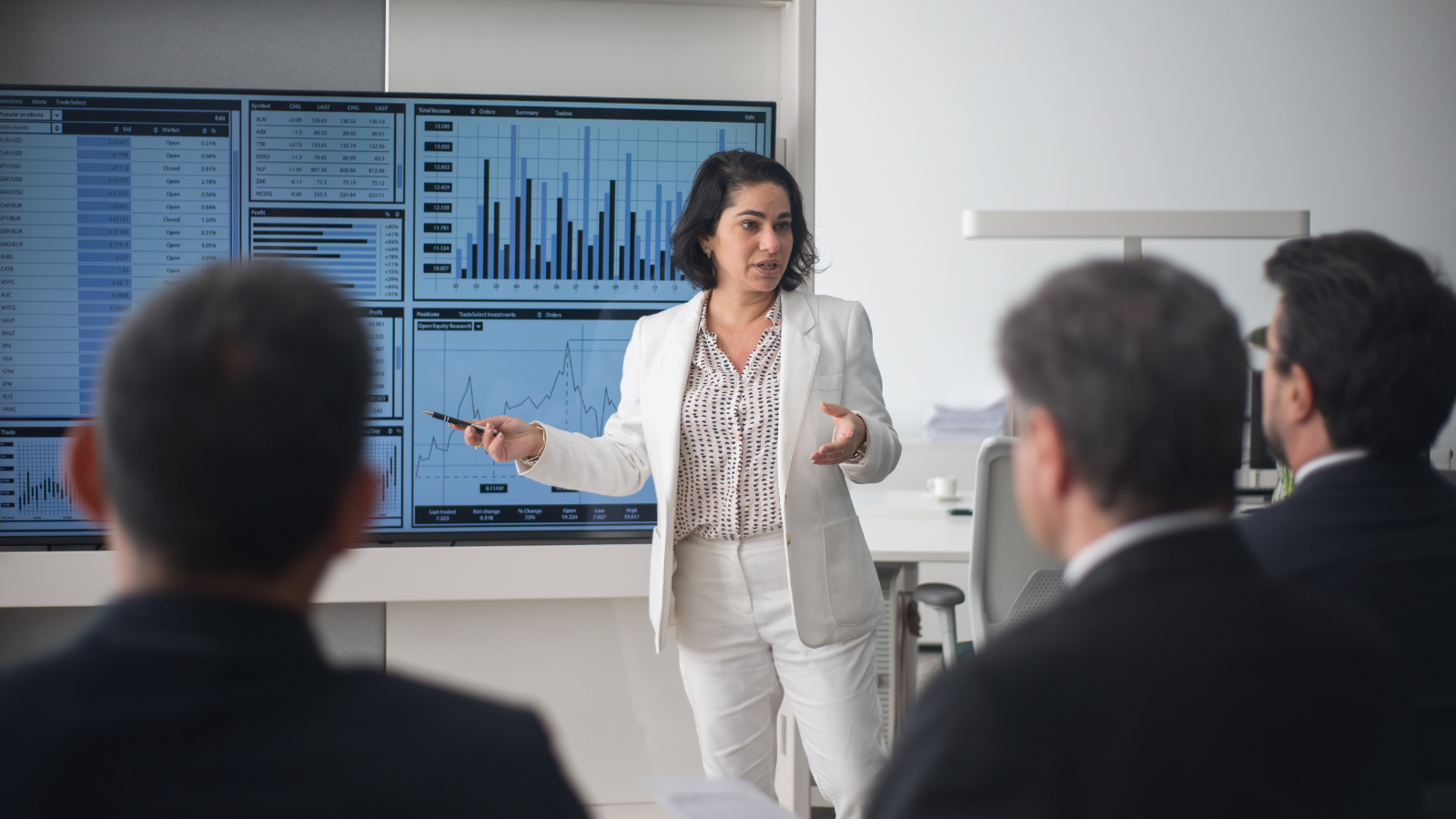
Process improvement is a fundamental practice within project management that involves evaluating existing processes to identify opportunities for enhancement and optimize outcomes. It focuses on refining workflows, increasing efficiency, and achieving better results. With this understanding, a process improvement consulting firm consists of experts who specialize in analyzing current processes, implementing proven frameworks for continuous improvement, and aligning processes with overarching business objectives to drive long-term success. What Does a Process Improvement Consulting Firm Do? A process improvement consulting firm provides a range of services aimed at optimizing business operations and driving efficiency. Some key examples include: • Process Documentation: They assist businesses in thoroughly documenting their processes, ensuring consistency, repeatability, and reducing the risk of errors. Clear documentation enables smoother operations and easier onboarding of new employees. • Strategic Process Optimization: Consultants provide expert recommendations on enhancing processes by identifying inefficiencies, improving resource utilization, and aligning operations with strategic business goals. • Customer Experience Enhancement: By analyzing existing workflows, they help businesses refine their processes to improve customer satisfaction, ensuring a seamless and efficient customer journey. • Problem-Solving and Innovation: They introduce structured methodologies, such as Lean or Six Sigma, to help organizations proactively address challenges, streamline workflows, and foster a culture of continuous improvement. • Technology Integration: Consultants evaluate and recommend tools or automation solutions that can enhance process efficiency, reduce manual effort, and support scalability. • Change Management Support: They guide businesses through the transition of implementing new processes, ensuring smooth adoption, minimizing resistance, and maximizing long-term success. • Performance Measurement: By establishing key performance indicators (KPIs), they enable businesses to monitor progress, track improvements, and make data-driven decisions for sustained growth. When Should a Business Consider Working with a Process Improvement Consulting Firm? Businesses often turn to process improvement consulting firms when they encounter challenges that hinder growth, efficiency, and overall performance. Some key indicators that it may be time to seek professional assistance include: o Stagnant Growth and Uncertainty: When a business struggles to scale or lacks a clear path forward, expert guidance can help identify inefficiencies and implement strategies to drive sustainable growth. o Persistent Process Inefficiencies and Bottlenecks: If operations are frequently slowed down by recurring inefficiencies, delays, or workflow bottlenecks, a consulting firm can provide insights and solutions to streamline operations. o Misaligned Technology Investments: When businesses invest in technology and personnel but still face process challenges, it often indicates that underlying processes are not well-defined or optimized for automation. Consultants help ensure processes are solidified before implementing technology solutions. o Cross-Departmental Communication Gaps: Poor communication and coordination between departments can lead to misunderstandings, redundant work, and delays. Process improvement specialists can create frameworks that enhance collaboration and operational alignment. o Low Employee Productivity and Engagement: If employees struggle to perform efficiently due to unclear workflows, manual processes, or a lack of streamlined procedures, consulting firms can introduce best practices to enhance productivity and job satisfaction. o Manual and Outdated Processes: Businesses relying on time-consuming, manual processes often find it difficult to keep up with competition. Process improvement consultants can introduce automation and standardization to increase efficiency. o Compliance and Quality Control Challenges: Ensuring compliance with industry regulations and maintaining quality standards can be challenging without well-structured processes. A consulting firm can assist in developing and maintaining compliance-ready workflows. What Should a Business Owner Look for in a Process Improvement Consulting Firm? When selecting a process improvement consulting firm, it's essential to evaluate several key factors to ensure you partner with the right experts for your business needs. Consider the following: • Proven Track Record and Transparency: Look for a firm that openly shares details about their previous work. Explore their website for client case studies, testimonials, and reviews to gain insights into their experience, the quality of their work, and how they have successfully helped other businesses achieve their goals. • Industry Expertise and Qualifications: Ensure the consulting firm has a team of qualified professionals with expertise in areas such as project management, Lean methodologies, Six Sigma, operational excellence, change management, and business process reengineering. Their knowledge should align with your industry-specific challenges and objectives. • Strong Communication and Alignment with Business Needs: Effective communication is crucial for a successful process improvement initiative. Choose a firm that takes the time to understand your unique business challenges and goals, while demonstrating the ability to clearly articulate solutions and guide your team through each phase of the improvement journey. • Customized Approach and Flexibility: Avoid firms that offer a one-size-fits-all approach. Instead, seek consultants who tailor their strategies to your business's specific processes, culture, and long-term objectives to ensure sustainable improvements. • Technology and Tools Expertise: If your business is considering automation or digital transformation, ensure the consulting firm has experience integrating technology solutions that align with your operational needs and can recommend tools that enhance efficiency and scalability. What Are the Benefits of Working with a Process Improvement Consulting Firm? Partnering with a process improvement consulting firm offers numerous advantages that can positively impact your business's operations and long-term success. Key benefits include: o Enhanced Business Stability and Clarity: A consulting firm provides a comprehensive understanding of your current processes, helping you recognize how they impact various departments and contribute to overall business performance. This clarity fosters greater operational stability and informed decision-making. o Identification of Improvement Opportunities: Through expert analysis, you’ll gain valuable insights into areas requiring enhancement and develop a clear roadmap to address inefficiencies. Consultants bring fresh perspectives and proven methodologies to optimize your workflows. o Access to Specialized Expertise: Leveraging the knowledge of experienced professionals allows you to navigate complex process challenges with confidence. Consultants provide guidance on best practices, industry standards, and strategies tailored to your business needs. o Cost Reduction and Resource Optimization: Streamlining processes helps eliminate waste, reduce operational costs, and improve resource allocation. This leads to more efficient use of time, technology, and personnel, ultimately boosting profitability. o Improved Customer Satisfaction: Enhanced processes lead to faster response times, fewer errors, and more consistent service delivery. As a result, customers experience higher quality interactions, which can increase loyalty and retention. These are just a few of the many ways businesses experience significant improvements when partnering with a process improvement consulting firm. If you're currently exploring options for the right consulting partner, we’d love to connect and discuss how we can support your business goals. Schedule a call with us to see if we’re the right fit for your needs. Not ready for a call just yet? Visit our Process Improvement page to learn more about our services and how we can help streamline your operations.
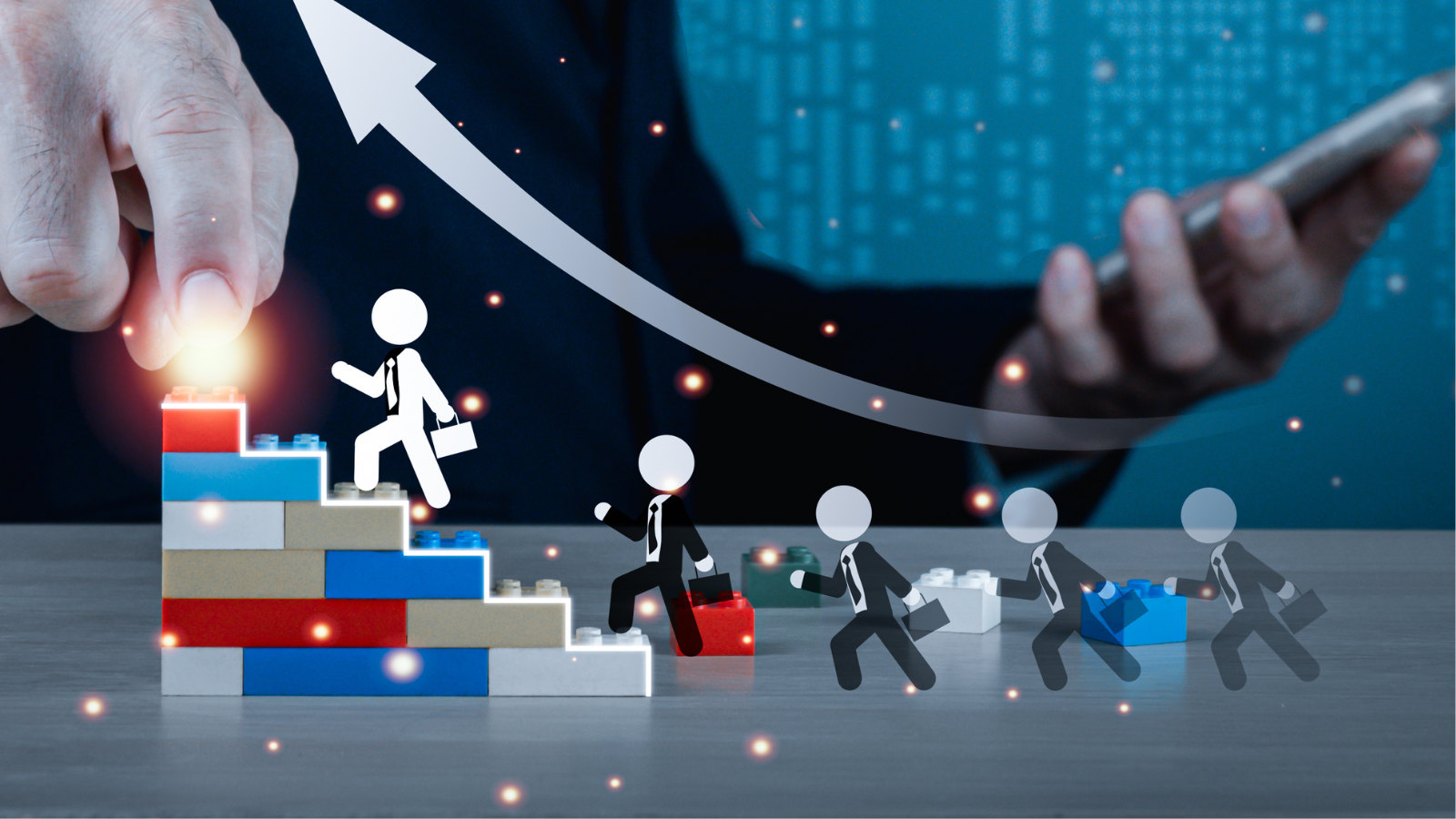
When and Why to Use a Process Improvement Consultant Businesses today face a wide array of challenges, made even more complex by the rapid pace of technological advancements. Operational inefficiencies, misaligned processes, and outdated workflows can hinder growth and negatively impact the bottom line. This is where a Process Improvement Consultant can make a significant difference. At Brewster Consulting Group, we believe process improvement is not just a task—it's a strategic initiative that can unlock hidden potential within your organization. To start, what is process improvement? Process improvement is often a partner to Project Management. In many organizations, PI and PM are treated as two separate functions, but they're essentially both project management practices, each with a focus on delivering different outcomes. Process Improvement focuses on evaluating and refining specific processes to deliver a specific, and measurable result. Project Management often focuses on broader enterprise change initiatives and is focused on delivering projects on-time, on-budget, and with the intended outcomes. In Process Improvement, established methodologies are usually applied to critical organizational processes to identify opportunities for improvement, error reduction, or an enhancement to the customer experience. Eliminating waste (such as time, resources, or money) is also a major target of PI initiatives. For example, in the manufacturing industry, process improvement might involve streamlining production lines to minimize downtime and reduce material waste. In the healthcare sector, it could mean redesigning patient intake processes to improve efficiency and reduce wait times. According to a recent Forbes article , the ultimate goal of process improvement is to optimize business strategies, making them more efficient. In doing so, it enhances the experiences of various stakeholders, such as customers, employees, and suppliers, creating a ripple effect of value throughout the organization. With this in mind, a process improvement consultant helps businesses bridge the gap between strategy and execution. So, what exactly does a process improvement consultant do when working with a business? A process improvement consultant engages in activities aimed at optimizing a company’s operations. The starting point is always a thorough assessment of the current processes, workflows, and day-to-day operational actions that define how the business operates. You cannot improve a process if you do not understand its current-state. By analyzing existing systems, identifying inefficiencies, and implementing targeted improvements, consultants play a pivotal role in driving a company’s operational excellence and long-term success. You might be wondering about the specific, tactical steps a Process Improvement Consultant will take when working with your company. We can’t speak for everyone, but if you work with one of our Process Improvement Consultants, we will begin by conducting a thorough assessment of the company’s processes. This involves stakeholder interviews, process mapping, and KPI definitions. We recently completed an engagement where we interviewed 38 stakeholders and process mapped 18 critical processes, complete with KPI definitions. This comprehensive evaluation pinpoints opportunities to optimize efficiency, scalability, and increased margins. By collaborating closely with leaders across the organization, we can collect data, analyze it in conjunction with the processes, and provide detailed reports and actionable recommendations based on the findings. In the engagement I referenced earlier, we helped migrate critical process data to Snowflake, and then build a KPI dashboard in Power BI, so we could understand how the process was currently performing and gauge future improvements. Here are some other specific examples of what this work may involve: Developing streamlined workflows for both department-specific activities and the organization as a whole to enhance efficiency and alignment. Facilitating cross-functional meetings with upper management and frontline employees to gain a comprehensive understanding of process goals, execution methods, and areas needing improvement. Implementing automation tools to reduce manual tasks and improve process accuracy and speed. Conducting time-motion studies to measure task efficiency and identify bottlenecks in workflows. Designing and managing process simulation models to test potential improvements before implementation, minimizing disruption and risk. Analyzing key performance indicators (KPIs) to track process performance and assess the success of implemented changes. These efforts collectively help organizations optimize their operations and achieve measurable improvements in performance and efficiency. By now, you should have a clearer understanding of the focus areas for a process improvement consultant. As mentioned earlier, these professionals utilize a variety of methodologies to achieve their goals. Below, we’ve outlined a few key approaches to help you become familiar with their core principles: Six Sigma : This methodology aims to minimize variations in products or services by relying heavily on statistical data to evaluate whether processes are performing optimally or require improvement. Two key methods under Six Sigma include: DMAIC (Define, Measure, Analyze, Improve, Control) : Focused on improving existing processes. DMADV (Define, Measure, Analyze, Design, Verify) : Geared toward creating new processes or products. Total Quality Management (TQM) : A company-wide focus on quality improvement by involving all employees in the process. Lean Manufacturing : Aims to eliminate waste (time, resources, money) while maximizing value to the customer. Kaizen (Continuous Improvement) : A philosophy of making small, incremental improvements over time to enhance processes. PDCA (Plan-Do-Check-Act) : A cyclical framework for testing and implementing process changes effectively. 5 Whys Analysis : A problem-solving technique that identifies root causes by repeatedly asking "Why?" about an issue. Business Process Management (BPM ): A structured approach to designing, analyzing, and optimizing an organization’s workflows for improved efficiency. How do you know if your business could benefit from a process improvement consultant? And what should you look for in a qualified professional for this role? First, if you answer "yes" to any of the following questions, it may be time to consider working with a process improvement consultant: 1. Are your customers frequently experiencing the same problem or raising similar complaints? 2. Are most of your processes still manual, or have you struggled to implement automation? 3. Is there a lack of effective communication and collaboration between departments? 4. Have you observed a decline in the quality of employee work? 5. Are you consistently falling short of your business goals? 6. Does your current technology support your business effectively, or are you encountering difficulties in managing or utilizing it? If these issues resonate, the next step is to find the right consultant to address them. What qualities and experience should you look for in a solid process improvement consultant? Key Skills and Qualifications: -Strong communication and interpersonal skills: They will need to engage with employees across all levels of the organization to understand challenges and share solutions effectively. -Excellent time management: Staying on top of deadlines and ensuring their work doesn’t add to existing operational delays. -Problem-solving expertise: Tackling complex issues and identifying root causes is a core part of their role. -Technical proficiency: They should have the skills necessary to analyze data and implement solutions effectively. Some examples include: -Data analysis and interpretation -Project management experience -Lean Six Sigma training or certification -Proficiency in tools like Visio, Excel, PowerPoint, and other process management software A great process improvement consultant listens carefully to your concerns, communicates clearly about what they need to make the project a success, and ultimately leaves your business in a stronger position. With their guidance, your organization can not only resolve immediate challenges but also build a foundation for ongoing improvement. We hope this article has given you a clearer understanding of what a process improvement consultant is, what they do, and what to look for when hiring one. If you think your organization could benefit from a partnership with a Process Improvement Consultant, we’d love to help! Reach out to us today, and let’s start improving your processes .
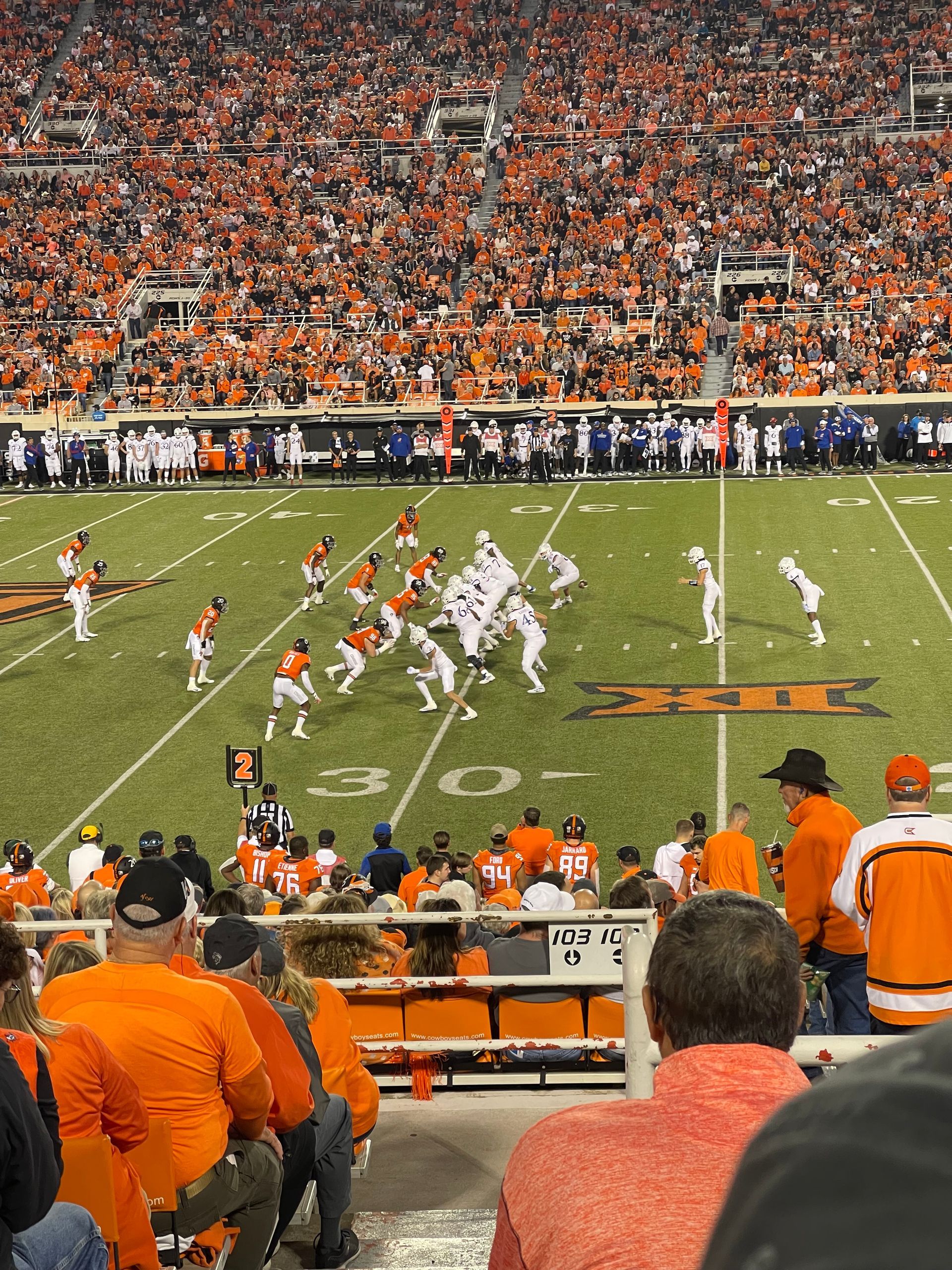
As the college football playoff unfolds , fans are captivated by the precision, strategy, and execution that separate championship teams from the rest. Last night, I was watching Ohio State vs. Texas. Texas was in position to tie the game late in the fourth quarter. On 2nd & Goal from the 1, instead of running the ball downhill behind one of the best offensive lines in America, they decided to pitch the ball outside, and they lost 7 yards as a result. This was likely the nail in the coffin as two plays later a strip sack returned for a touchdown made it a two touchdown Ohio State lead with 2 minutes to play. Now, Texas coach Steve Sarkisian knows way more than I will ever know about football, so I really shouldn't be questioning the play call. However, it just felt like a strange call in that scenario given the strength of the Texas offensive line, and the elite speed of the Ohio State defense. Now, Ohio State will play Notre Dame for the national title (TV Executives Rejoice) and Texas is done for the year. However, with the benefit of hindsight, it certainly would have been beneficial in that moment for Sark to remember that Ohio State might have the fastest defensive roster in the country, and running outside against elite speed is often a recipe for disaster. Football season is my favorite time of year. My wife and I, both Oklahoma State University alumni, share a passion for the sport and attend games regularly with season tickets. Above you'll see me and my daughter at one of her first OSU games—a snapshot of our little family tradition. But what is my point, in this discussion about football? Why am I bringing up the Texas second down call from last night? Well, I'm glad you asked. It's because, like business, college football is very complex. Behind every play call there is usually a very specific game plan that has been derived from hours of meticulous game film analysis. Coaches and players obsess over game tapes, using them to refine their strategies, identify weaknesses, and exploit opportunities. What if I told you that in the world of business, data is the equivalent of game film for football?? For businesses, data provides insights into operations, competitors, and customers, much like game film illuminates the strengths and weaknesses of a football team. Let’s dive into this analogy, exploring how data can transform a business’s performance just as game film shapes the destiny of a football team vying for the championship. Analyzing Your Team: Understanding Internal Strengths and Weaknesses Football Insight : Coaches meticulously study practice film to evaluate their own players. They identify who hustles during every rep, who understands the playbook, and who is consistently out of position. Each player is graded to assess their strengths and weaknesses, influencing decisions on starting lineups and rotations. Business Parallel : Businesses must evaluate their internal teams using performance data. Whether it’s salespeople, welders, service providers, or machinists, analyzing KPIs such as productivity, quality, and adherence to protocols helps identify top performers and areas for improvement. Key Actions: Track individual and team performance metrics. Use KPIs to highlight strengths and gaps in execution. Develop coaching plans for underperformers and reward high achievers. By studying their own "practice film," businesses can make strategic decisions about promotions, training, and even resource allocation to ensure that the right people are in the right roles. If you want your business to win, you need to build the best roster that you possibly can. Scouting the Competition: Understanding Market Position Football Insight : Opponent film reveals key players and tendencies. Coaches identify star performers—like an elite wide receiver or dominant defensive end—and plan their strategy accordingly. Whether it’s double-teaming a threat or adapting offensive schemes, understanding the opponent gives teams a competitive edge. Business Parallel : Businesses can gain similar advantages by analyzing competitors’ data. Metrics like customer satisfaction scores, pricing structures, and sales trends offer insights into where competitors excel and where they fall short. This level of information allows you to strategically choose how you want to position yourself in the market. Key Actions: Conduct competitive benchmarking to assess market position. Identify gaps in your offerings and decide whether to invest in improvement or adjust pricing strategies. Use customer feedback to understand where competitors are outperforming you. Strategic decisions rooted in competitor analysis—just like game plans formed from film—help businesses stay ahead in the market. Game Planning: Building a Data-Driven Strategy Football Insight : Coaches build gameplans by combining insights from practice and opponent film. They create playbooks that maximize their team’s strengths and exploit their opponent’s vulnerabilities. Teams that execute these plans well often dominate those that rely on intuition alone. It's also important to note that each gameplan is built for a specific opponent. You don't recycle the same gameplan for every game, that's a losing strategy. Business Parallel : Data-driven businesses craft strategies based on insights from internal and external analysis. This involves: Identifying key trends and opportunities. Aligning resources to leverage strengths and address weaknesses. Developing proactive responses to potential market shifts. Building a unique winning strategy for each major competitor. Key Actions: Use dashboards and analytics tools to monitor real-time performance. Implement predictive analytics to anticipate customer needs and market trends. Align operational goals with the data insights to ensure execution matches strategy. Identify top competitors, conduct SWOT analysis for each, and build a plan on how you compete and win against each one. A well-prepared business strategy, just like a game plan, wins by design rather than by chance.
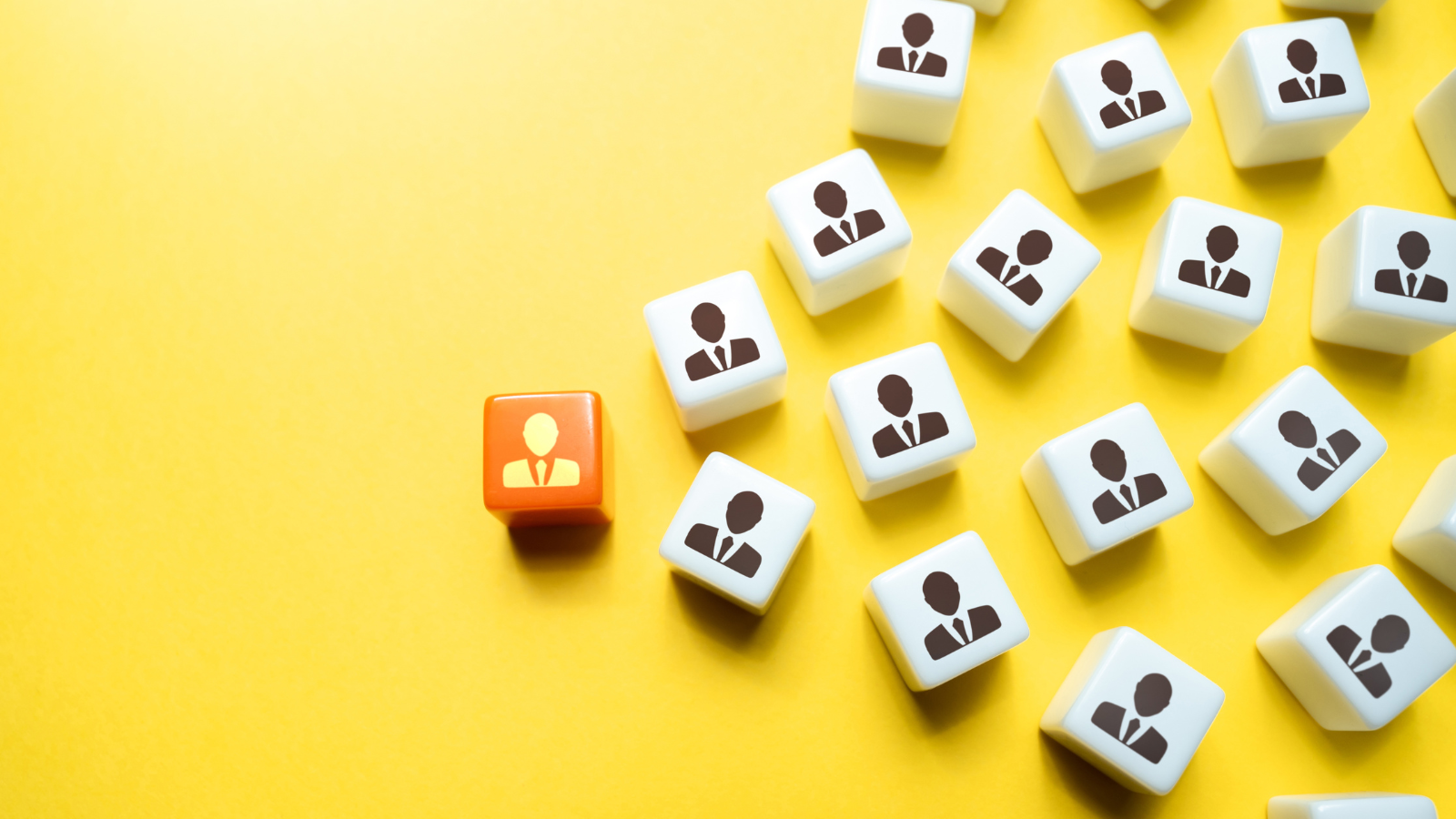
The rise of fractional leadership has become a defining trend in today’s business world. Companies of all sizes are increasingly turning to fractional leaders, such as Fractional Chief Data Officers (CDOs), Fractional COOs (Chief Operating Officers), and Fractional Project Managers , to address critical leadership needs. This approach is particularly valuable as businesses grow from small enterprises into medium-sized organizations or navigate periods of transition and rapid growth. But why is this shift happening? What makes fractional leadership so appealing, and why has it been so successful? Let’s explore. The Growing Demand for Fractional Leaders Demand has skyrocketed in recent years, increasing by over 100% year-over-year . According to an article on CFO.com , this dramatic rise stems from several factors, including higher employee turnover and a surge in executive resignations. These challenges create leadership gaps that are difficult to fill quickly, prompting businesses to seek alternative solutions, such as fractional hires. Fractional leaders provide a quick and effective solution for these gaps, allowing companies to maintain momentum without compromising on expertise or leadership quality. Addressing the Skills Gap One of the key factors driving the popularity of fractional leadership is the growing skills gap across industries. More businesses are struggling to retain or find full-time leaders with the specialized expertise they require. A recent article on Trainingindustry.com highlights that many businesses are experiencing significant budget reductions for leadership development, with the average cut in these budgets reaching approximately 70% over the past year . This reduction, combined with a lack of emphasis on leadership training and development, has only exacerbated the skills gap. Fractional leaders provide a strategic solution to this challenge. These professionals come equipped with the necessary skills to make an immediate impact, minimizing onboarding time and maximizing efficiency. Furthermore, fractional leaders often pursue opportunities to expand their knowledge and experience across industries, alleviating the burden on companies to provide ongoing training and development programs. The Rise of Fractional Leadership The trend of adopting this kind of leadership is expected to grow even further. A recent study on Vendux.org about the state of fractional leadership revealed that 25% of businesses in the U.S. currently utilize fractional executives, a number projected to rise to 35% by 2025 . Companies are leveraging fractional talent not only to address leadership gaps but also to keep pace with evolving technologies and market demands—all while maintaining cost efficiency. Why Fractional Leadership Works The success of fractional leaders lies in their ability to deliver: Specialized Expertise: They bring years of experience in specific domains. Immediate Impact: With minimal onboarding required, they can hit the ground running. Cost Efficiency: These roles provide high-caliber leadership without the expense of full-time hires. This flexible approach empowers businesses to navigate periods of transition, scale efficiently, and remain competitive in a rapidly changing environment. Is Fractional Leadership Right for Your Business? For businesses facing leadership gaps or struggling to find the right talent, fractional leadership offers a viable and effective solution. Whether you need a Fractional Chief Data Officer (CDO) to guide your data strategy, a Fractional COO (Chief Operating Officer) to streamline operations, or a Fractional Project Manager to ensure successful project execution, fractional leaders provide the specialized expertise, structure, and strategy you need to scale, manage transitions, and move forward with confidence. If you’d like to explore how fractional leadership could benefit your business, we encourage you to check out our blogs and videos on this topic. At Brewster Consulting Group , we’re passionate about helping businesses thrive through flexible and impactful solutions. Book a discovery meeting with us today—we’d love to help you find the perfect fractional leader for your needs.
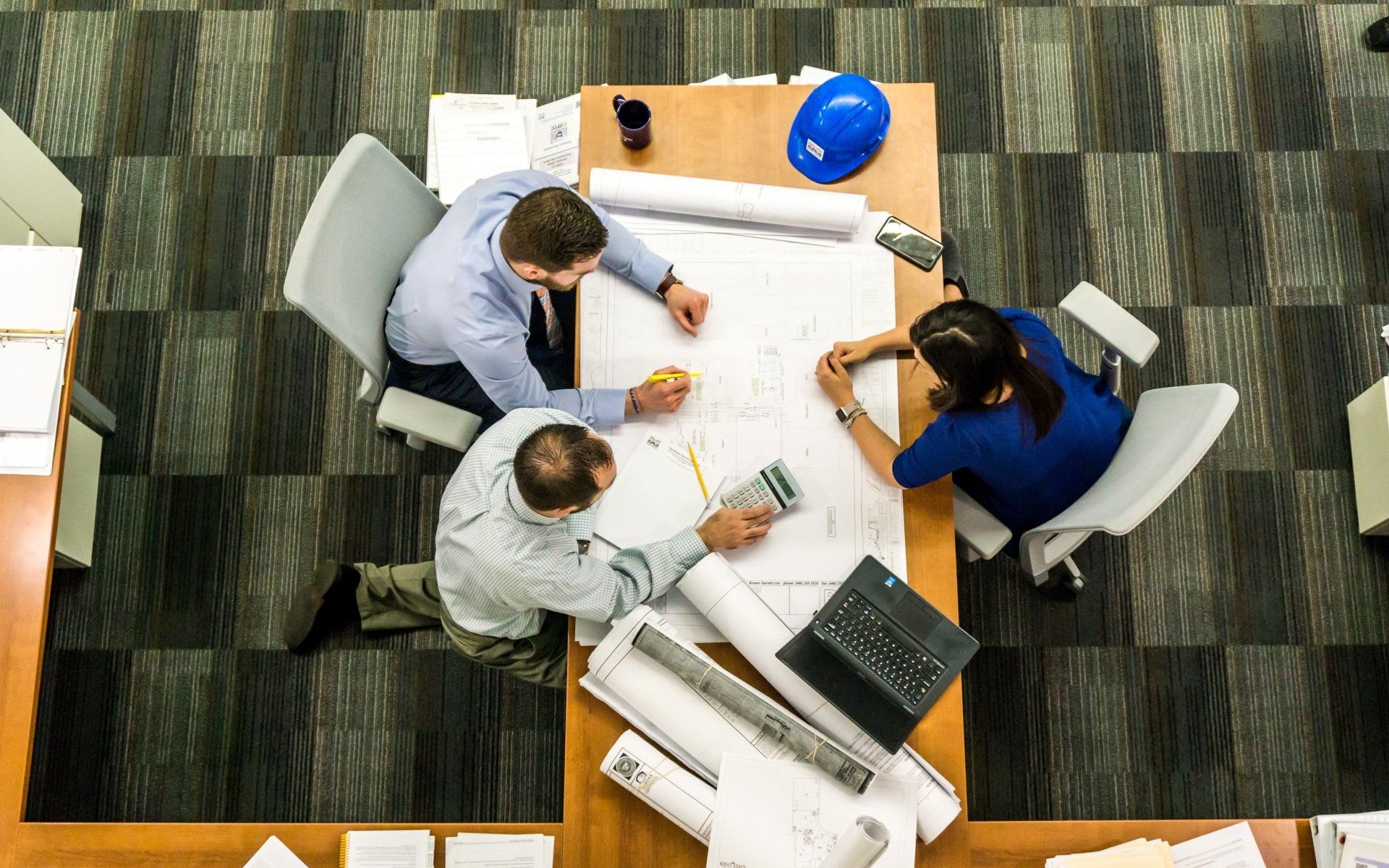
Executive Summary Project Management as a Service (PMaaS) is a flexible, scalable solution for businesses that need expert project management without committing to a full-time hire. PMaaS, also known as fractional project management, allows organizations to access experienced project managers on-demand to ensure their initiatives are completed on time, within scope, and on budget. This service is particularly beneficial for small and mid-sized businesses (SMBs), startups, and large enterprises seeking to optimize resources, reduce costs, and increase operational efficiency. By outsourcing project management functions, companies can focus on their core competencies while relying on experts to deliver critical projects effectively. This article delves into the essence of PMaaS, its advantages, and its practical applications, ensuring businesses understand why it is a game-changing solution. 1. What is Project Management as a Service (PMaaS)? Definition and Core Concept PMaaS provides organizations with access to professional project management resources on a flexible basis. It's an alternative name for fractional project management, where services are tailored to the client’s specific needs, allowing businesses to: Scale resources up or down based on project demands. Engage experienced project managers without long-term commitments. Ensure projects align with strategic goals. Key Characteristics of PMaaS On-Demand Expertise : Access to certified professionals with diverse industry experience. Cost Efficiency : Avoids the overhead costs associated with hiring full-time employees. Customizable Engagements : Services tailored to match project complexity and organizational needs. PMaaS bridges the gap between temporary staffing solutions and high-cost consulting firms, making it an ideal choice for companies seeking quality project execution without overextending their budgets. 2. Benefits of PMaaS for Organizations Enhanced Flexibility PMaaS enables businesses to respond swiftly to changing project requirements. Whether launching a new product, upgrading technology, or implementing organizational changes, PMaaS ensures you have the right resources at the right time. Access to Specialized Expertise Professional project managers bring industry best practices, frameworks, and methodologies such as Agile, Waterfall, or hybrid approaches. This expertise: Reduces project risks. Enhances efficiency. Drives better outcomes. Cost Savings Hiring a full-time project manager incurs significant costs, including salary, benefits, and training. PMaaS eliminates these expenses, offering: Pay-as-you-go models. Services tailored to your budget. No long-term financial commitments. Improved Focus on Core Business Activities With project management handled externally, internal teams can concentrate on strategic business functions. This ensures operational continuity while projects are managed seamlessly. Scalability As business needs evolve, PMaaS allows organizations to scale project management resources up or down. This ensures optimal utilization of resources during peak and low-demand periods. 3. Key Applications of PMaaS SMBs and Startups Small and mid-sized businesses often lack the resources to hire dedicated project management teams. PMaaS provides access to seasoned professionals to guide: Product launches. Process improvements. System implementations. Large Enterprises Enterprises can use PMaaS to complement in-house capabilities, especially during periods of: High project volume. Organizational restructuring. Mergers and acquisitions. Technology Upgrades and Transformations PMaaS ensures seamless planning and execution of: ERP system implementations. Cloud migrations. Digital transformation initiatives. 4. How PMaaS Differs from Traditional Project Management Engagement Model Traditional project management involves hiring full-time staff or consultants. PMaaS offers: Short-term or long-term engagements. Flexible pricing models. On-demand services. Resource Allocation Unlike traditional models, PMaaS allows businesses to allocate resources only when needed. This minimizes downtime and optimizes costs. Focus on Outcomes PMaaS providers are outcome-driven, emphasizing measurable results such as: Meeting project deadlines. Achieving key performance indicators (KPIs). Delivering within budget constraints. 5. Selecting the Right PMaaS Provider Assessing Business Needs Identify project requirements, including: Scope and complexity. Desired outcomes. Budget constraints. Pain Points & Bottlenecks. Evaluating Providers Look for PMaaS providers with: Proven industry experience. Certified PMP project managers. Positive client testimonials. Experience with a number of different systems and project types. We hope you'll consider us if you get to this stage, but even if you don't you should look for this level of experience. Setting Clear Expectations Establish detailed agreements, including: Defined project scope. Communication protocols. Success metrics. Measuring Performance Use regular check-ins and post-project reviews to ensure alignment with goals. Conclusion and Actionable Takeaways PMaaS offers a modern, flexible approach to managing projects, blending the benefits of fractional project management with scalable solutions for businesses of all sizes. By leveraging PMaaS, organizations can: Access expert project managers without long-term commitments. Achieve cost savings while maintaining high-quality project execution. Enhance operational focus and agility. Next Steps for Businesses: Evaluate Needs : Identify projects that could benefit from external project management expertise. Research Providers : Seek out experienced PMaaS providers with strong credentials (Like Brewster Consulting Group). Start Small : Engage in a pilot project to assess the value of PMaaS for your organization. With PMaaS, businesses can navigate today’s complex project landscapes efficiently and effectively, positioning themselves for long-term success.
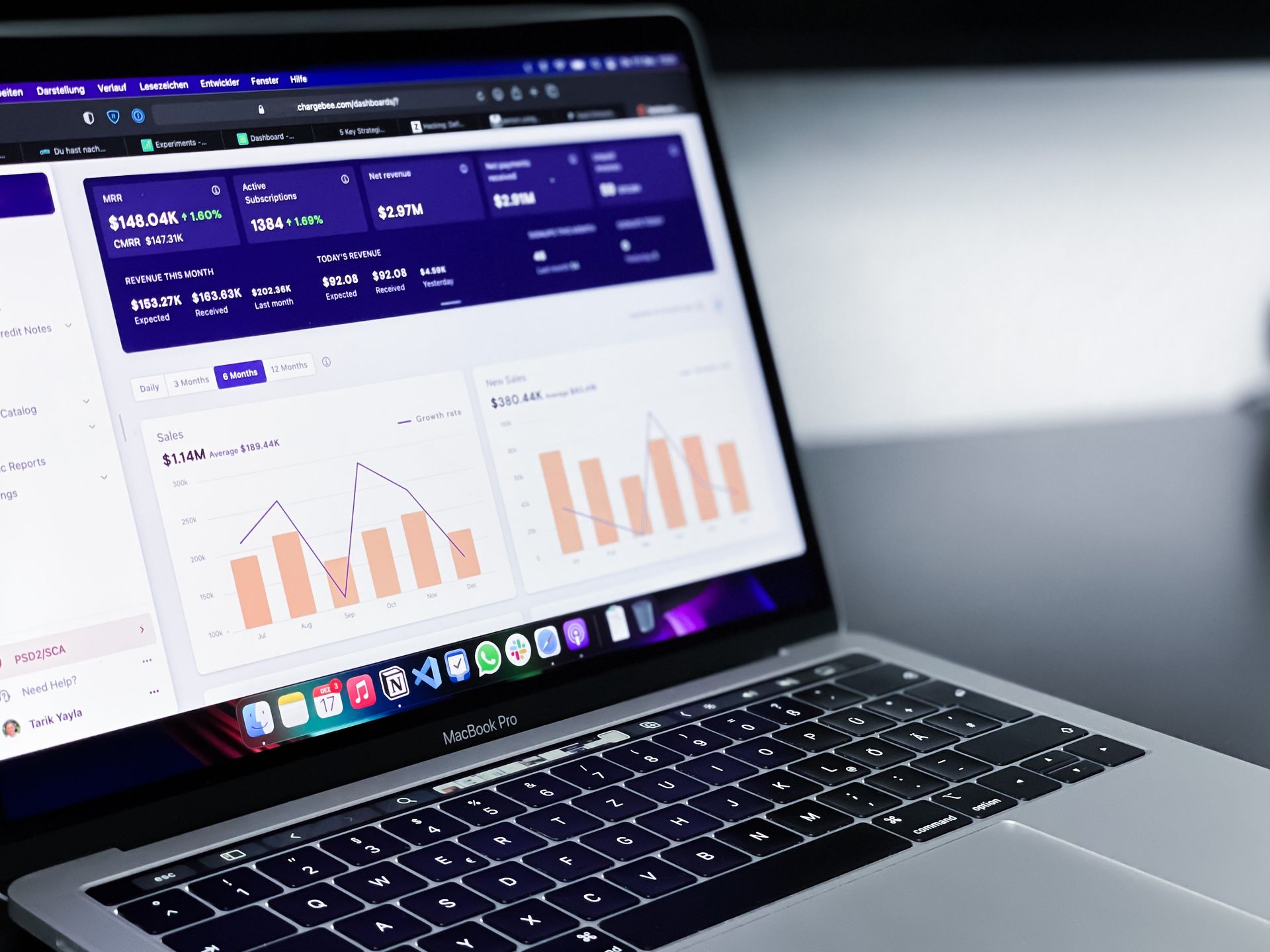
Executive Summary In an age where data drives decision-making, effective data visualization is a critical skill for organizations aiming to extract meaningful insights from their information. Data visualization consulting empowers businesses to present complex datasets in clear, actionable formats, enhancing decision-making, communication, and strategy development. One of my favorite texts on the subject is Dona M. Wong’s " The Wall Street Journal Guide to Information Graphics ." I frequently reference this publication when working through visualizations for clients. This article uses that text as a reference and explores the essential elements of data visualization consulting, including its benefits, methodologies, tools, and best practices. 1. The Importance of Data Visualization 1.1 Why Visualize Data? Data visualization converts raw data into a visual context, such as charts, graphs, and maps. This transformation helps: Simplify Complexity : Visual tools distill intricate datasets into digestible insights. Enhance Retention : Studies show visuals improve comprehension by 400% compared to text alone. Drive Decision-Making : Decision-makers can identify trends, outliers, and patterns faster. 1.2 Real-World Applications Data visualization consulting has proven invaluable in various sectors: Healthcare : Visualizing patient outcomes to improve treatment protocols. Finance : Monitoring investment performance through dashboards. Retail : Analyzing consumer behavior for targeted marketing. Dona M. Wong emphasizes clarity and simplicity: “Avoid clutter. Simplicity is not about removing information but about making it accessible.” This principle is foundational for effective consulting. 2. The Consulting Process 2.1 Discovery Phase Effective consulting begins with understanding the client’s needs: Objective Identification : Clarify goals, such as trend analysis or performance tracking. Audience Analysis : Design visuals tailored to the end-users’ technical expertise. Data Audit : Assess the quality, completeness, and relevance of datasets. 2.2 Design and Development During this phase, consultants: Select Visualization Types : Choose charts or graphs that best represent the data. Wireframe Prototypes : Create mockups to align with client expectations. Incorporate Feedback : Refine designs through iterative reviews. 2.3 Implementation and Training To ensure sustainability: Deploy Dashboards : Implement interactive tools such as Power BI or Tableau. Train Teams : Equip clients with the skills to maintain and update visuals. Iterate : Once people are able to interact with your dashboards, they will undoubtedly have thoughts on things to add, work with them in an iterative fashion to craft it into the perfect business tool. 3. Key Tools and Technologies Popular Platforms Data visualization consultants use a variety of tools, each suited for specific needs:
Want To Get Our Content Directly in Your Inbox?
Email Us
For general inquiries & questions,
contact us via email.