Lean Thinking Made Simple: Spotting Waste in Any Industry
What Does Lean Mean?
By now, you've probably heard the term "lean"within your business organization, in conversations with industry leaders, or perhaps seen it in a post online. At first glance, it might seem like an odd concept or one that’s difficult to apply to business. However, understanding lean—and more importantly, the negative impact of "lean waste"—is critical to improving operations and maximizing value. Let’s start by defining a few key terms and then dive into the different types of waste that lean principles aim to eliminate.
What Do We Mean by Lean?
When we talk about "lean," whether in the context of lean thinking, lean management, or lean business, we're referring to the practice of maximizing value and profit while minimizing waste. At its core, lean is about eliminating anything that doesn’t add value for the customer—be it a process, task, or activity.
Understanding Waste in Lean
In lean methodology, "waste" is defined as anything that doesn’t directly contribute value to the customer. This could include inefficient processes, unnecessary tasks, or poorly utilized resources. Lean identifies eight types of waste that can arise during the lifecycle of a process. Originally developed in the manufacturing industry, these principles are now applied across various sectors to improve efficiency and productivity.
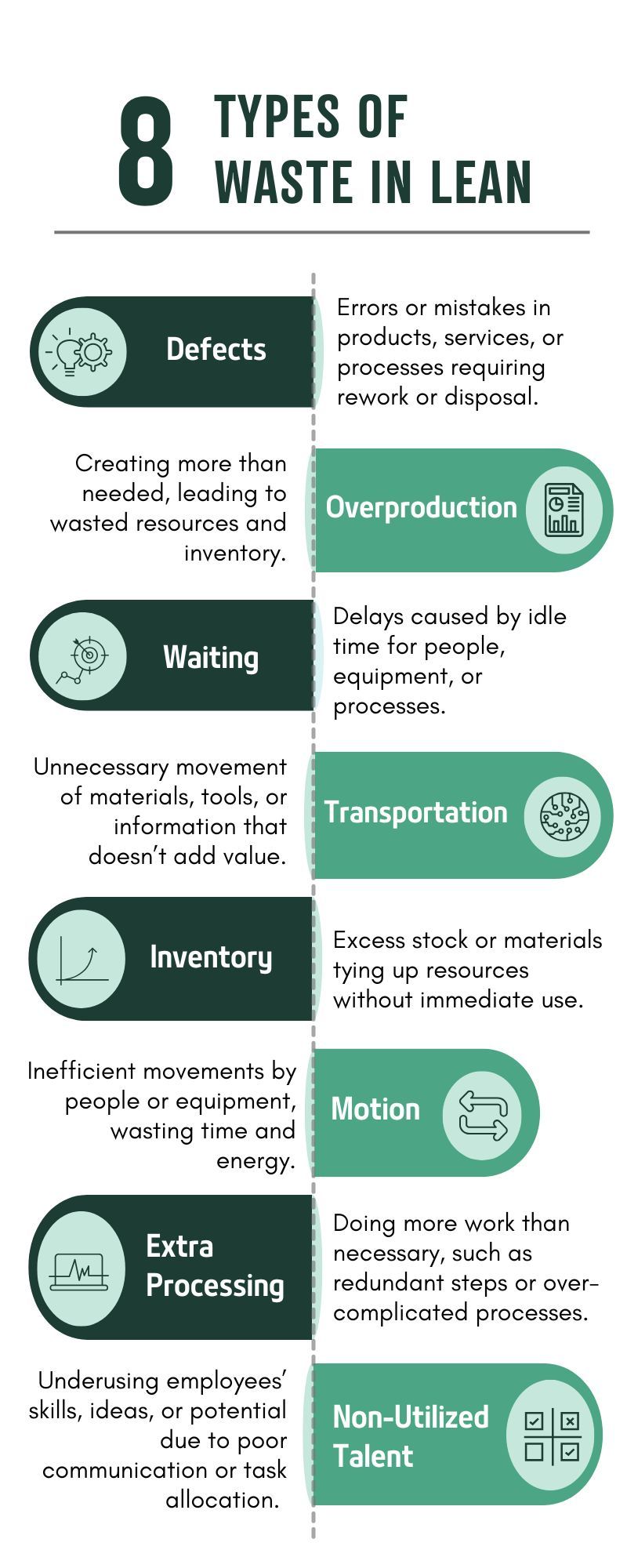
The 8 Types of Waste in Lean
Defects - Defects occur when products or components are flawed, improperly measured, or unsuitable for use. Defects not only waste materials but also lead to wasted time and money as products often cannot be reused.
Example: A batch of products fails quality checks due to incorrect specifications, requiring costly rework or disposal.
Solution: Implement rigorous quality control measures and root cause analysis to prevent defects at the source.
Overproduction - Overproduction happens when more products are created or processes completed than needed. While the intention might be to "get ahead," it often results in unnecessary inventory, defects, and wasted resources.
Example: Producing 500 units when the customer only ordered 300.
Solution: Adopt just-in-time production methods to align output with demand.
Waiting - Waiting waste can affect both people and equipment. It occurs when materials, supplies, or tools aren’t available when needed, or when processes are delayed due to bottlenecks.
Example: Workers standing idle because materials haven’t arrived.
Solution: Streamline processes to ensure smooth handoffs and minimize bottlenecks.
Transportation - Excessive movement of materials, equipment, or people leads to wasted time and effort. This doesn’t contribute to adding value and can even wear down machinery unnecessarily.
Example: Moving raw materials multiple times before they reach the production line.
Solution: Optimize layouts and minimize unnecessary transportation by strategically locating workstations.
Inventory - Excess inventory ties up capital and creates inefficiencies. It often results from overproduction or over-purchasing and can lead to further waste like defects or damage.
Example: Stocking large quantities of raw materials that sit unused for months.
Solution: Implement inventory control systems like just-in-time ordering to reduce excess stock.
Motion - Inefficient motion refers to unnecessary movements—like workers repeatedly reaching for specific equipment or traveling back and forth between workstations. These actions waste time and energy.
Example: Employees walking across a facility multiple times to retrieve tools.
Solution: Arrange tools and workstations ergonomically to minimize motion.
Extra Processing - Extra processing includes unnecessary steps, redundant tasks, or using overly complex equipment or procedures.
Example: Requiring multiple approvals for a simple order or double entering the same data into different systems.
Solution: Simplify processes and reduce redundancies through automation and process standardization.
Non-Utilized Talent - This waste occurs when employee potential is underutilized. A lack of communication or involvement between management and employees can lead to missed opportunities for innovation and improvement.
Example: Frontline workers with process improvement ideas are ignored.
Solution: Foster open communication and empower employees to share their insights and participate in decision-making.
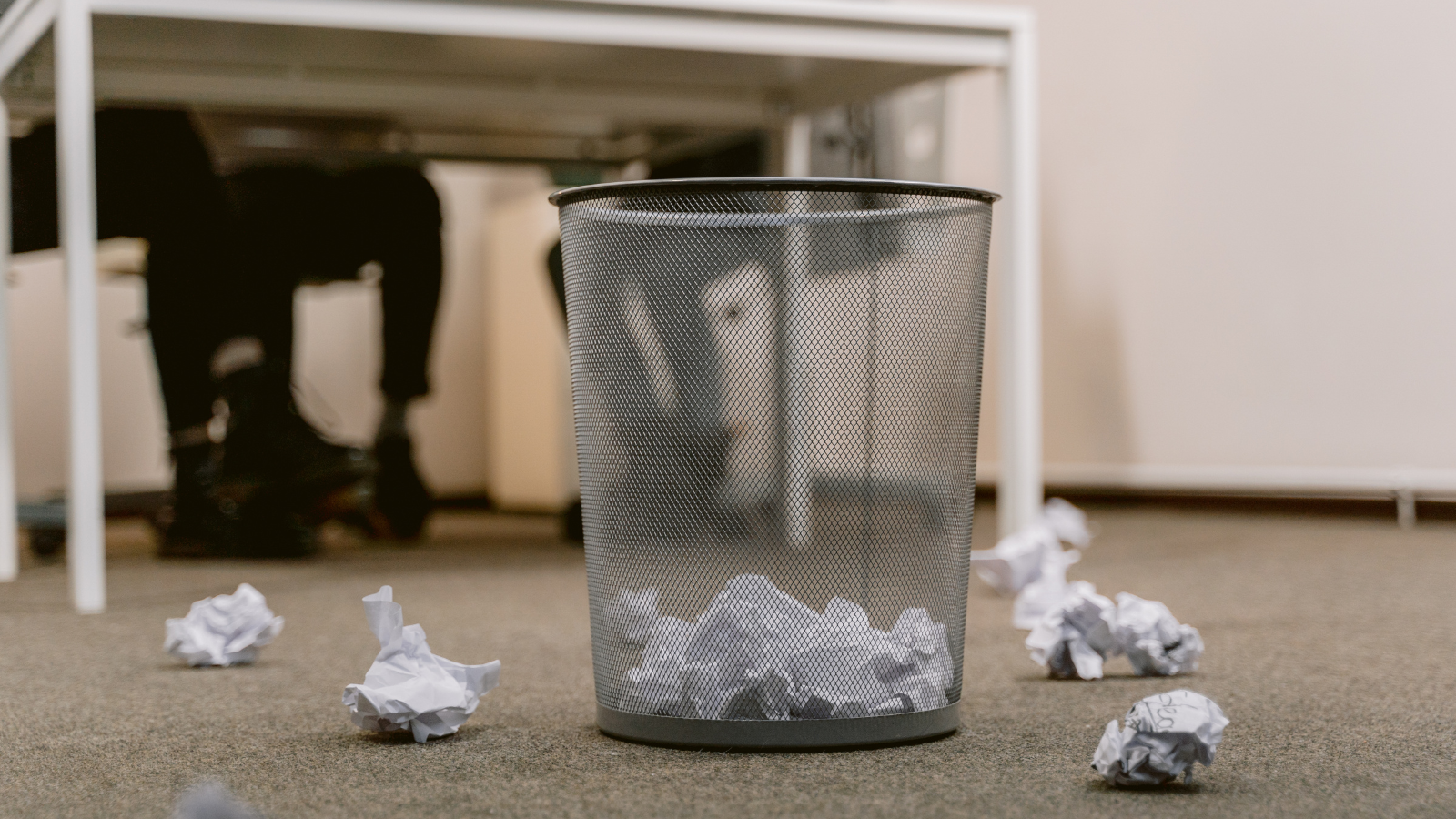
Examples Beyond Manufacturing
While lean principles originated in manufacturing, their relevance extends far beyond the factory floor. Businesses across industries—whether in healthcare, retail, IT, or professional services—can experience and address these eight wastes. Here’s how these wastes might appear in non-manufacturing contexts, along with actionable examples for each.
Defects:
What It Looks Like: Errors in a customer invoice, incorrect data entered into a system, or typos in marketing materials. These mistakes can lead to lost time, rework, and potential reputational damage.
Example: A financial services firm sends a client an incorrect monthly statement, requiring customer support to spend hours correcting it.
Solution: Use automated tools to validate data inputs and double-check critical deliverables.
Overproduction:
What It Looks Like: Creating more reports, materials, or content than is necessary. This often leads to wasted resources and clutter.
Example: An IT team generates weekly reports with data no one reviews or uses.
Solution: Align deliverables with actual business needs and eliminate redundant tasks or reports.
Waiting:
What It Looks Like: Employees waiting for approval, software to load, or other team members to complete their portion of a project.
Example: A marketing team delays a campaign launch because they're waiting for upper management to approve minor design edits.
Solution: Streamline approval workflows and set clear timelines for decision-making.
Transportation:
What It Looks Like: Moving materials, tools, or information excessively between locations or departments. This includes inefficient handoffs in digital systems.
Example: A retail business requires physical paperwork to be sent between stores and headquarters, delaying important decisions.
Solution: Digitize processes and establish centralized communication tools to reduce unnecessary movements.
Inventory:
What It Looks Like: Overordering supplies, stocking unused office equipment, or having excessive backlogs of work.
Example: A consulting firm prints large quantities of outdated brochures that no longer reflect their services.
Solution: Shift to digital materials and adopt a just-in-time strategy for ordering supplies.
Motion:
What It Looks Like: Employees wasting time searching for files, tools, or resources.
Example: A customer service representative spends extra minutes navigating a poorly organized CRM system to find customer information.
Solution: Implement better organization and streamline access to frequently used tools or files.
Extra Processing:
What It Looks Like: Adding unnecessary steps to a process, such as duplicating data entry, over-complicating workflows, or requiring excessive documentation.
Example: A legal team requires three separate approvals for minor contract revisions, causing delays in client delivery.
Solution: Simplify processes by reducing non-essential steps and leveraging automation where possible.
Non-Utilized Talent:
What It Looks Like: Employees not being empowered to contribute ideas, being under-challenged, or misaligned with their strengths.
Example: A healthcare facility has nurses spending hours on data entry tasks instead of patient care, underutilizing their expertise.
Solution: Delegate administrative tasks to support staff and involve employees in problem-solving initiatives.
Lean Thinking Across Industries
No matter your industry, the principles of lean can help you identify and address waste, saving time, money, and resources. Whether you’re streamlining operations in a tech startup, optimizing workflows in a healthcare organization, or refining processes in a retail business, understanding and mitigating these eight wastes is key to operational success.
Taking the First Step Toward Lean Efficiency
The journey to lean efficiency begins with identifying areas of waste in your processes. Acknowledging inefficiencies and understanding their impact is crucial. However, determining the next steps or addressing these inefficiencies can feel overwhelming.
That’s where expert guidance comes in. At Brewster Consulting Group, we specialize in helping businesses uncover and address waste using a structured framework tailored to their needs. We assist companies in identifying the root causes of inefficiencies and provide actionable roadmaps to eliminate waste, optimize operations, and prevent future issues.
Lean isn't just about cutting costs—it's about building sustainable, value-driven processes that benefit your business and your customers. Ready to transform your operations? Let’s get started.
Contact Brewster Consulting Group today to learn how we can help you achieve operational excellence through lean principles!
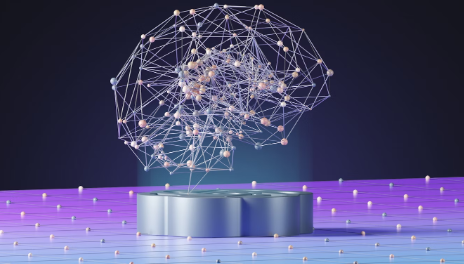
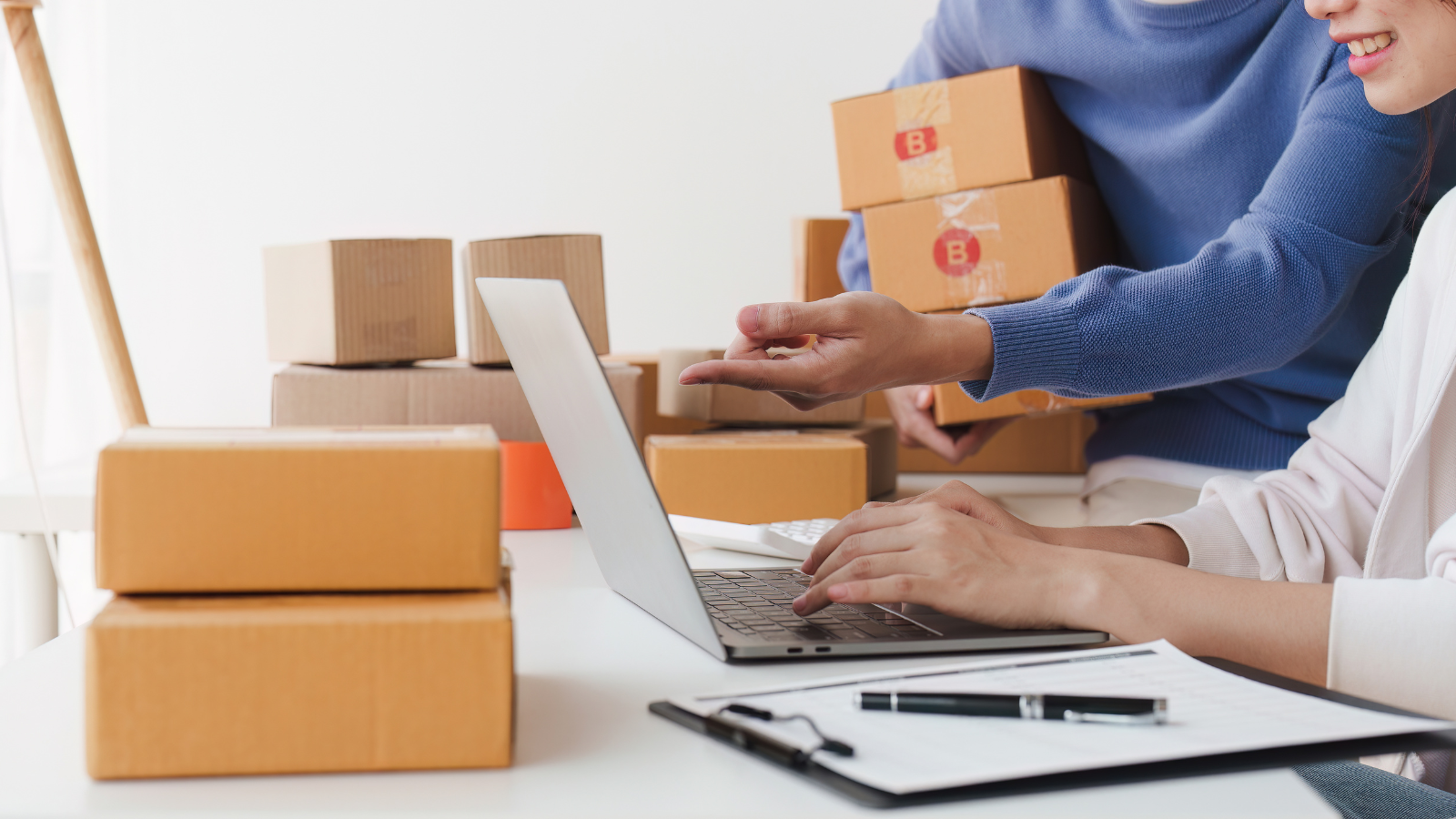
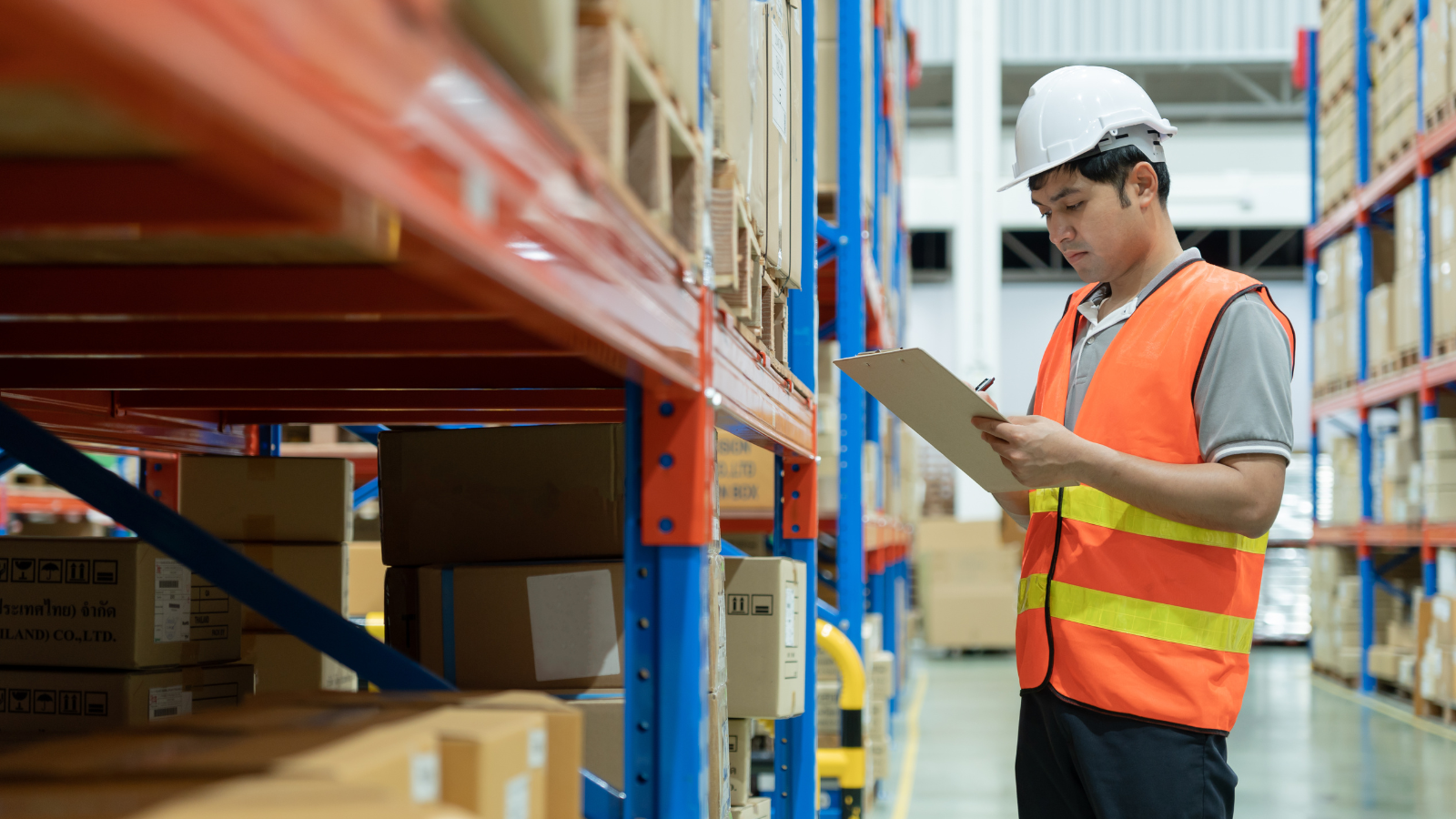
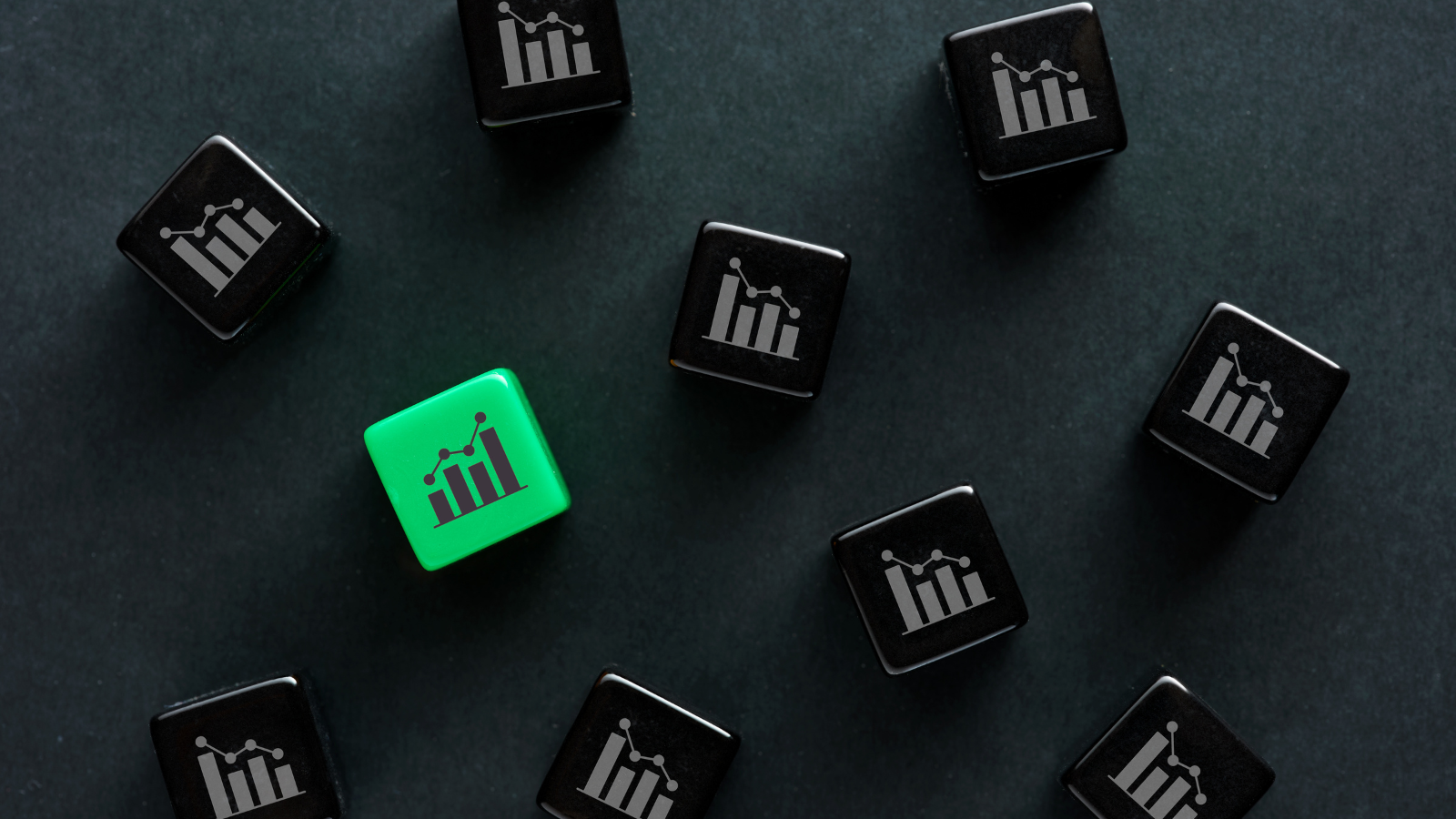
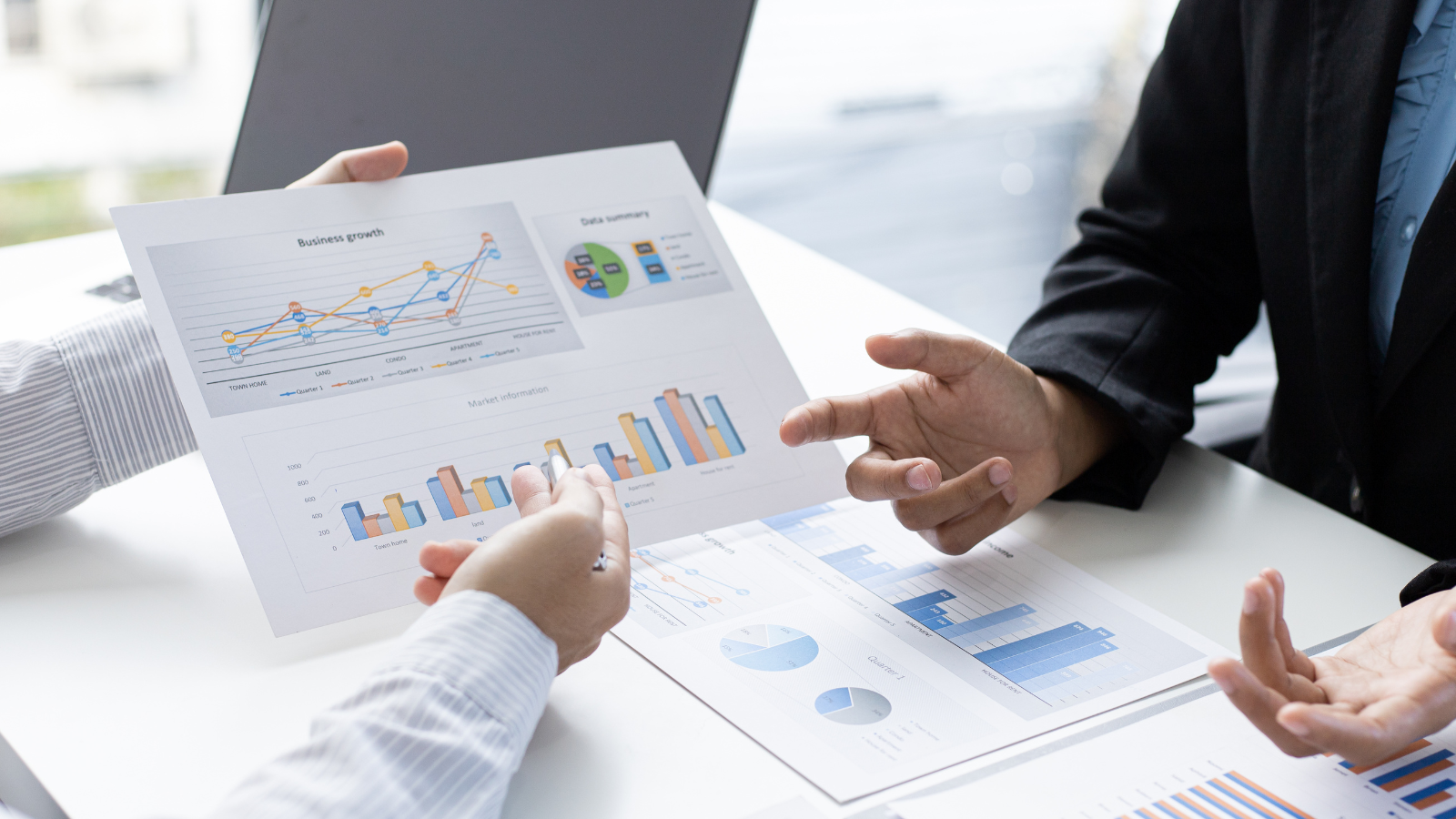
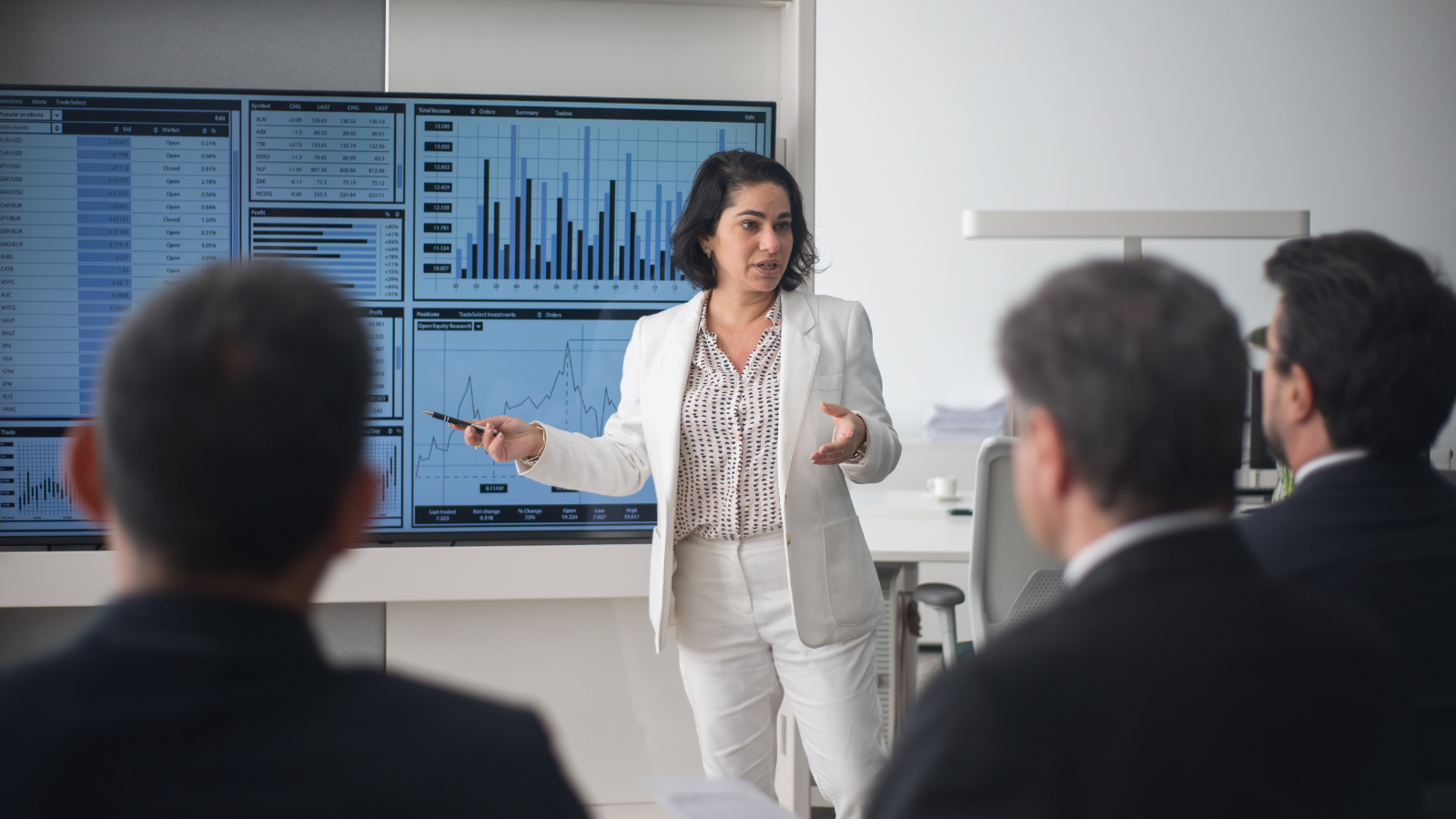
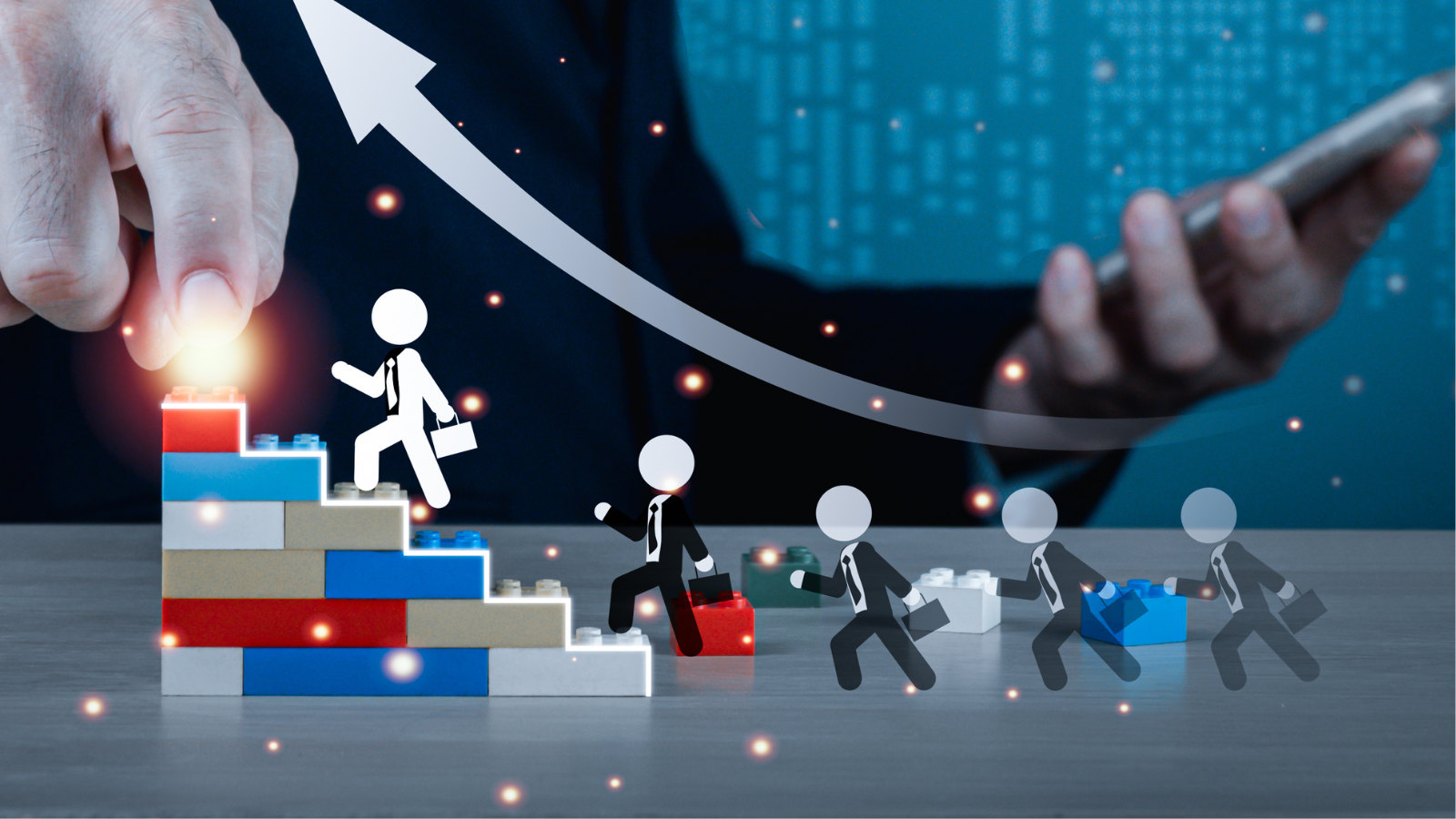
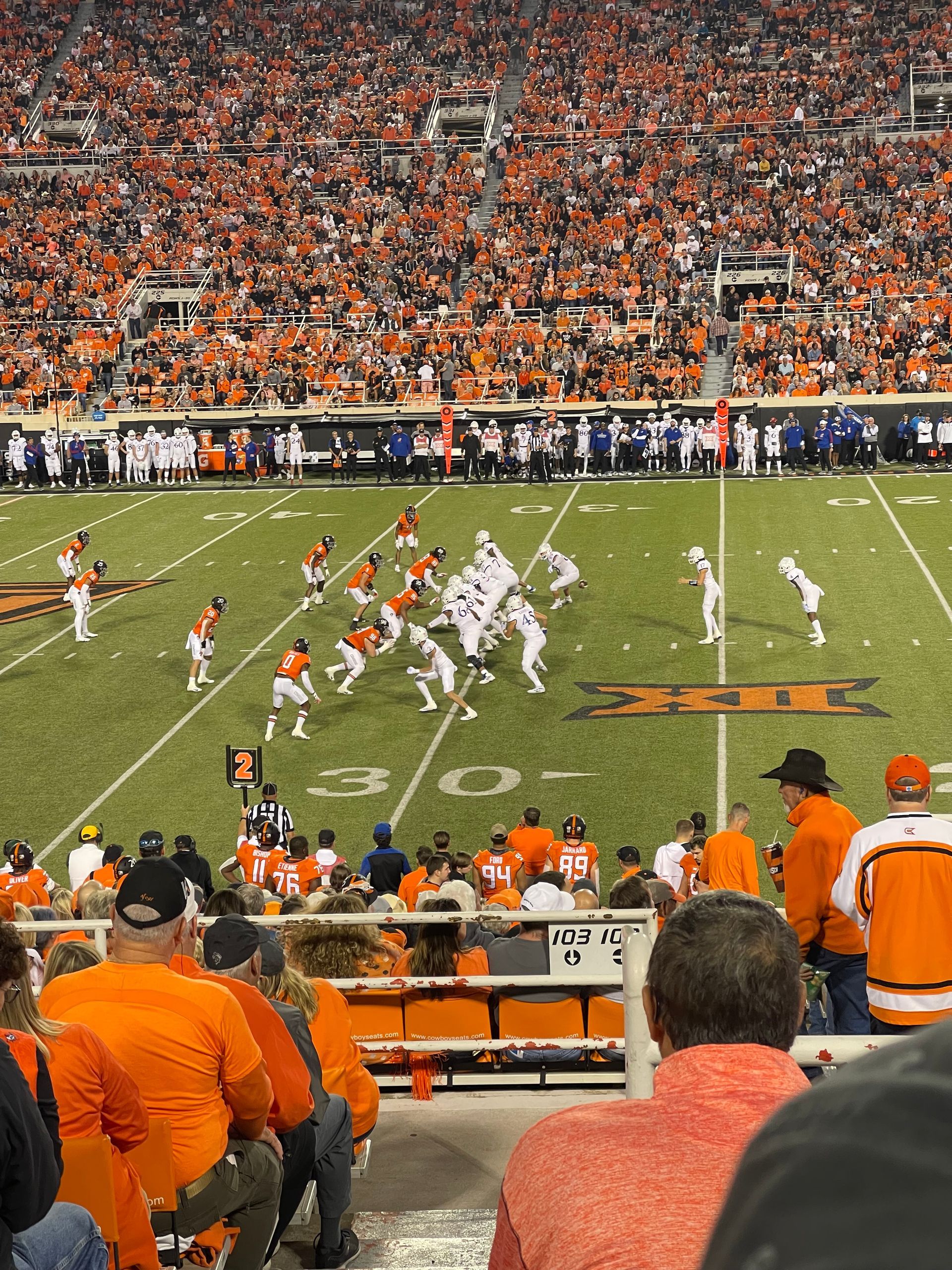
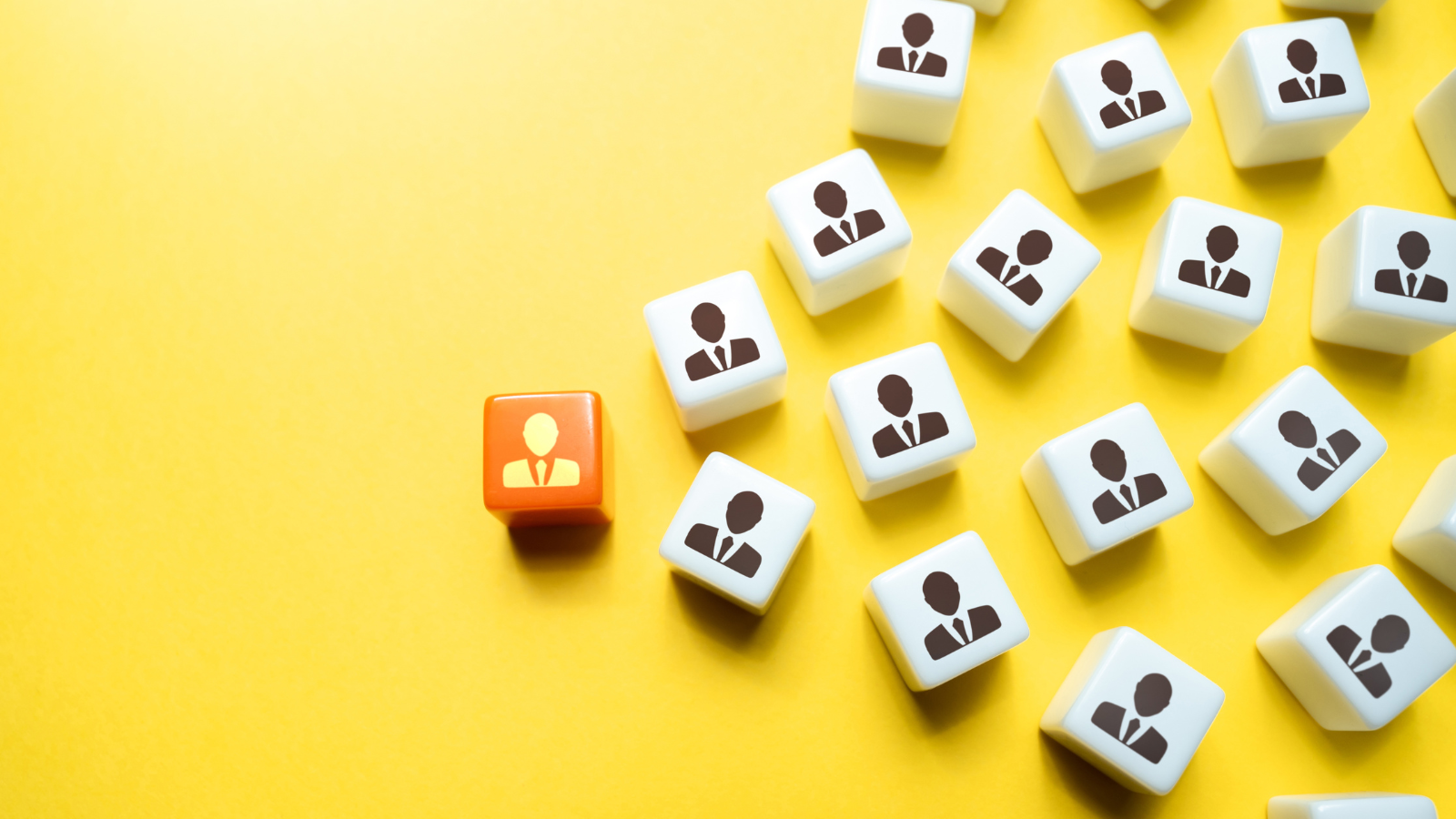
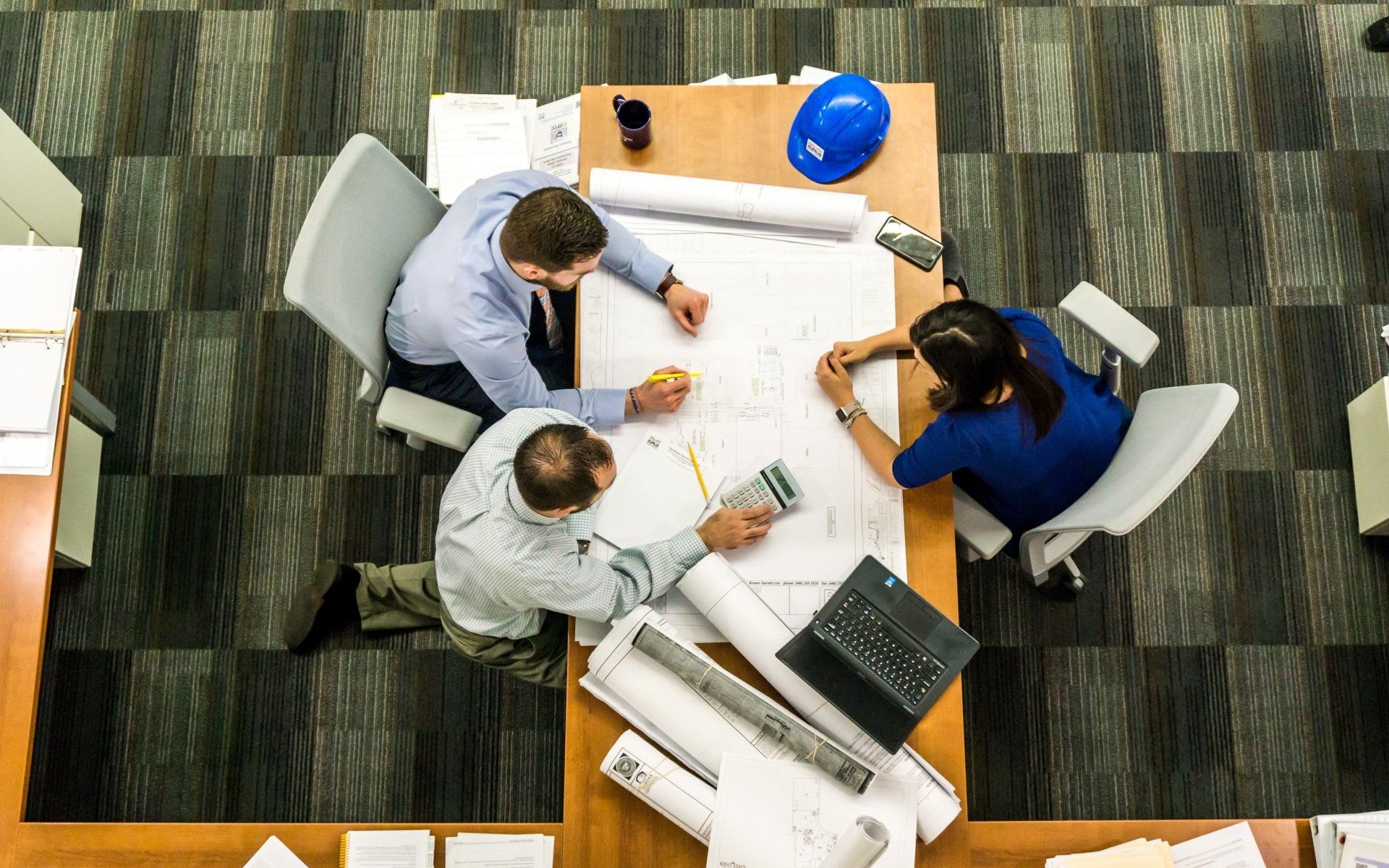